Mining comes with real risks. Equipment failures, falls, explosions, and exposure to harmful materials can lead to serious injuries or fatalities. Every incident can also cause long delays and financial losses. Preventing accidents is not just a moral responsibility — it’s a practical decision. That’s where mining safety training becomes essential. Workers who know how to identify hazards and act fast in critical situations help keep operations stable and efficient.
Investing in the right safety training solutions can reduce risks, improve employee performance, and ensure compliance with legal standards. Many companies still rely on outdated materials or occasional seminars, but modern training methods offer much more. They use real-world scenarios, digital tools, and data to make learning clear and repeatable.
Focusing on practical knowledge, not theory, allows workers to stay alert and prepared. Clear safety procedures and regular refreshers also reduce confusion during emergencies. For anyone managing a mining operation, upgrading safety training solutions is one of the most cost-effective ways to protect both people and profits. The rest of this article explains how to build a system that actually works.
The High Cost of Overlooking Safety
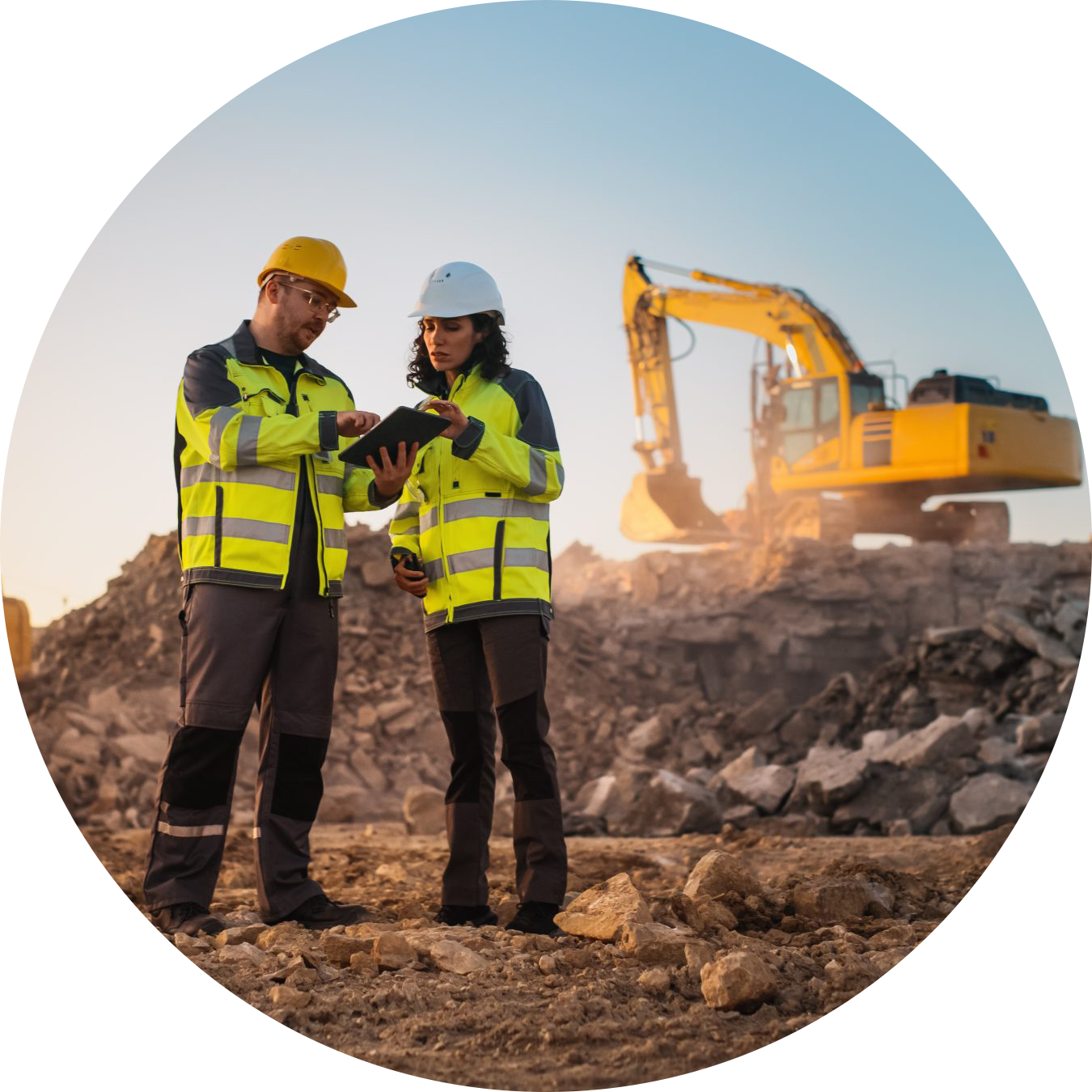
Mining is dangerous when safety is treated as a formality. One small error can trigger a chain of events that puts lives and operations at risk. Skipping proper instruction or using outdated materials opens the door to injuries, shutdowns, and major financial losses.
Even modern workplaces often miss the mark by relying on passive lectures instead of active virtual corporate training that reinforces action-based learning. Safety isn’t about memorizing rules — it’s about applying them when it counts.
Main consequences of poor training:
- Increased injuries. Workers make critical errors without up-to-date knowledge.
- Operational delays. Accidents bring everything to a stop.
- Regulatory trouble. Safety failures often trigger inspections and fines.
Accidents That Shaped the Industry
Mining history is filled with tragic examples that highlight what happens when safety is not a priority. Some of the worst disasters could have been avoided with the right procedures, clear communication, and regular safety drills.
In 2010, the Pike River Mine explosion in New Zealand killed 29 miners. Investigations revealed poor ventilation, ignored warning signs, and a lack of emergency plans. No proper hazard checks were in place. In the U.S., the 2006 Sago Mine explosion trapped 13 men. Communication systems failed, and emergency training was lacking.
Lessons learned from past events:
- Emergency plans must be specific. Generic instructions don’t help in real situations.
- Communication systems must work underground. Gaps in contact can cost lives.
- Workers must know chemical risks. In some incidents, exposure to gases made injuries worse — better chemical safety training could have reduced harm.
- Inspections must be regular. Unsafe conditions often develop slowly and get missed without routine checks.
Each major accident in mining history has led to new rules and higher standards. But even the best regulations are useless without training that helps workers understand and follow them every day.
How Downtime Impacts Profitability
Every time an incident occurs, production stops. It doesn’t matter whether it’s a small injury or a major accident because any event that removes people, equipment, or energy from the workflow affects the bottom line.
Unplanned downtime forces companies to pay for idle time, emergency services, and sometimes repairs or replacements. It also damages morale, which lowers productivity even after operations restart. Safety training prevents these interruptions by preparing workers to avoid or respond to hazards quickly.
Pivotal impacts of unplanned downtime:
- Delays in delivery. Customers and partners lose confidence when shipments are late.
- Increased costs. Overtime, replacements, and repairs add up fast.
- Lower output. Fewer hours of production mean reduced revenue.
- Higher insurance rates. Frequent accidents increase premiums.
Well-trained workers can spot and solve problems before they escalate. That stability translates into fewer shutdowns, better performance, and higher profits over time.
Hidden Costs: Legal, Reputational, and Human
Not all consequences of poor safety training are visible right away. Some costs show up months later in legal disputes, damaged reputations, and employee burnout. These outcomes are harder to measure but just as damaging to long-term performance.
Legal trouble often starts with a single missed safety check or poorly documented protocol. Injured workers may sue. Regulators may issue fines. Investigations can take months and disrupt daily operations. Lawsuits can drag on for years, draining both time and money.
Reputation also takes a hit. Clients, investors, and future employees pay attention to a company’s safety record. One major accident can scare off talent and reduce interest from serious partners.
Then there’s the human cost. When workers don’t feel safe, motivation drops. High turnover and low morale become common. Families suffer when accidents occur. Survivors often deal with trauma and stress long after the incident.
Main hidden costs to consider:
- Legal delays and lawsuits.
- Loss of public and industry trust.
- Mental and emotional strain on employees.
Avoiding these outcomes begins with intense, consistent training built into daily routines.
What Effective Mining Safety Training Looks Like
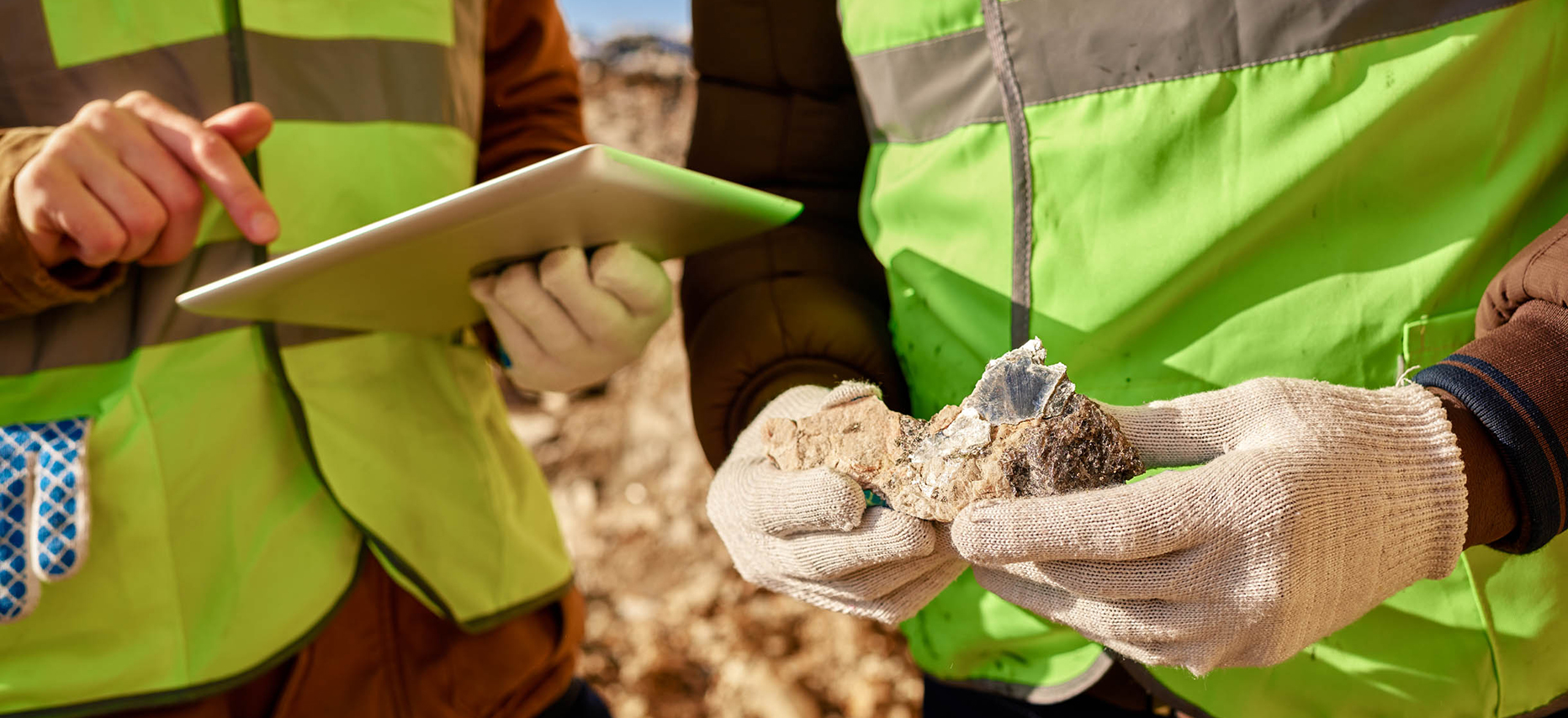
General reminders don’t replace proper instruction. A solid safety program explains what to do, how to do it, and why it matters. Each worker needs more than basic advice. Instead, they need training that fits the reality of their tasks. Good programs focus on clear instructions, repeatable steps, and targeted learning. That’s what separates real training from one-off talks. Hard skills training ensures that people are prepared to respond, not just stay informed.
Beyond Checklists: Interactive and Practical Learning
Written rules help, but they don’t prepare workers for real-world pressure. Effective safety training goes beyond lists and presentations. It gives people the chance to apply knowledge in ways that match their worksite.
Modern programs use technology to improve learning results. For example, VR warehouse training tools are being adapted to mining environments. Workers can walk through simulations of emergency scenarios, equipment handling, or hazard response without physical risk. This type of practice builds memory and helps them stay calm under stress.
Essential features of practical learning:
- Realistic simulations. People understand better when they can see and do.
- Immediate feedback. Workers improve faster when they know what needs fixing.
- Skill repetition. Doing tasks multiple times helps build confidence.
- Job-relevant tasks. Practice must reflect actual risks and daily duties.
Training works best when people stay engaged and the material sticks. Interactive learning ensures that workers remember what to do, not just what to say.
Tailoring Training to Risk Levels and Roles
Different jobs bring different risks. A welder faces hazards that a control room technician doesn’t. Effective training adjusts to each worker's actual duties instead of forcing everyone through the same process.
Programs built around tasks and risk levels allow each person to learn what’s most relevant. It also helps experienced staff stay sharp while new hires get the basics. Supervisors should receive leadership-focused content as well, including how to manage incidents and keep crews focused under pressure.
Effective role-based training includes:
- Custom content. Match lessons to each role’s daily tasks.
- Risk-based grouping. Prioritize training for high-exposure roles.
- Support materials. Provide quick references for complex jobs.
Applying this approach also supports engineering safety training, which requires more technical detail than general safety content. The better the alignment, the stronger the safety outcomes.
Frequency and Refreshers — The Key to Retention
One-time training sessions don’t work over the long term. People forget details quickly, especially if they rarely face emergency situations. Safety habits improve when key points are reviewed regularly and built into the work routine.
Short refresher sessions, regular drills, and quick updates help keep knowledge current. These don’t need to be long or disruptive. Even 10-minute reviews before shifts can make a difference. Repetition keeps procedures at the forefront of the mind and reduces hesitation in urgent moments.
Best practices for long-term retention:
- Scheduled refreshers. Plan monthly or quarterly sessions based on job risk.
- Microlearning. Use brief lessons that focus on one clear point at a time.
- Drills and walkthroughs. Practice builds comfort with fast decision-making.
- Tracking progress. Monitor who’s trained, when, and on what.
Consistent training creates routine, and routine leads to stronger, safer reactions on the job.
Need a functional mining safety training solution?
Modern Tools That Make Safety Training Stick
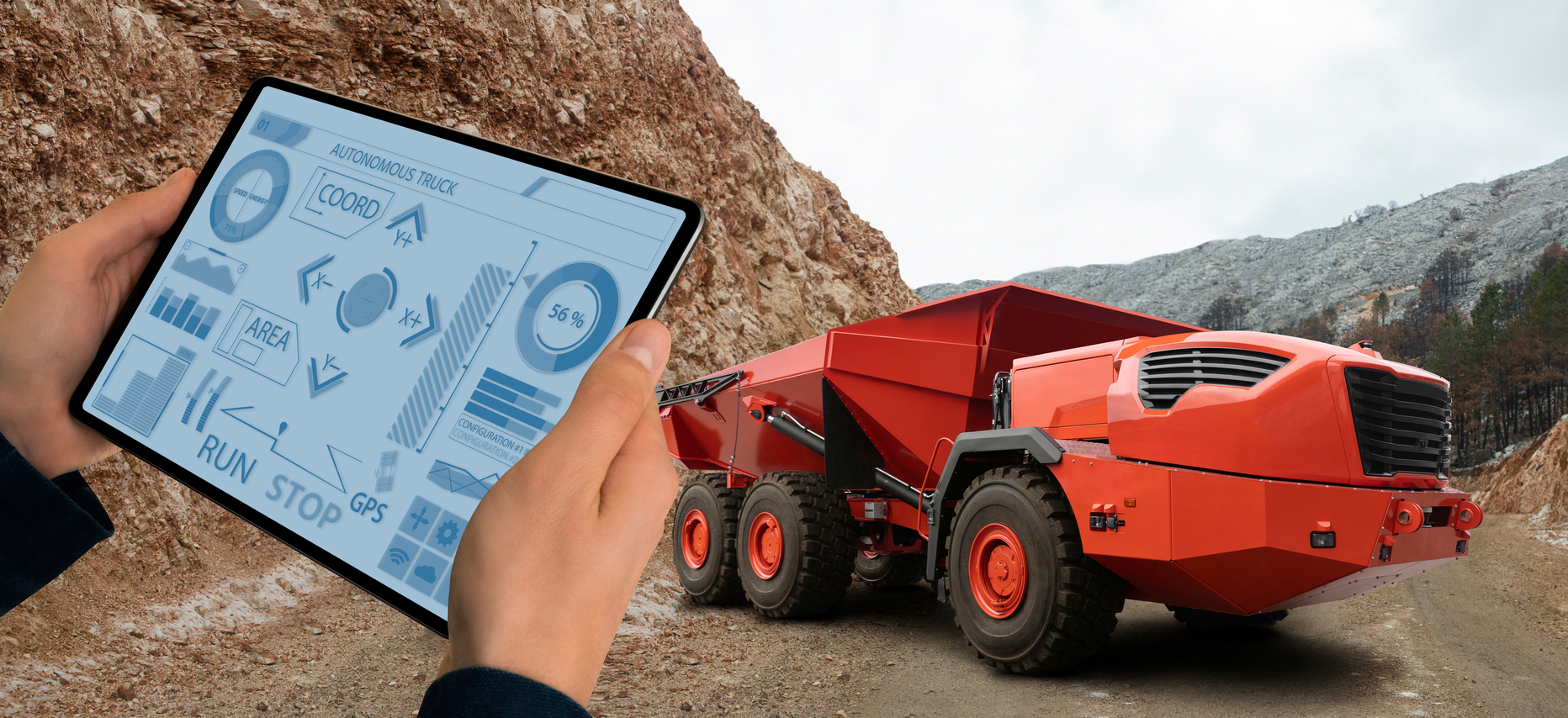
New tech has changed how safety training works. Workers don’t need to sit in long sessions to learn something useful. Now, they can practice on devices, get real-time feedback, and train in realistic environments without leaving the worksite. The best results come from using tools that match how people learn. Virtual reality safety training companies offer simulations that make safety tasks more straightforward to understand and easier to remember.
Simulation Tech and VR: Realistic, Risk-Free Learning
Simulations and virtual reality bring real job risks into a safe training space. Instead of reading about emergencies or watching slides, workers can interact with equipment, spot hazards, and practice response steps in a controlled digital setting.
This hands-on experience makes a big difference. It shortens the time it takes to learn and improves retention. People are more likely to remember what they’ve done than what they’ve read. In mining, this means safer decisions when they matter most.
Primary benefits of simulation-based training:
- Realistic decision-making. Workers respond as they would on-site.
- Repetition without danger. High-risk tasks can be practiced safely.
- Visual learning. Complex procedures are easier to grasp when seen in action.
- Faster skill development. Real-time feedback improves results.
Many virtual reality safety training companies now design content tailored to specific industries, including mining. These simulations can be adjusted to fit surface or underground operations, giving each team a practical edge. Using simulation tech, companies can raise safety standards without slowing down operations.
Mobile Learning and Microlearning for On-Site Access
Safety training doesn’t need to happen in a classroom. Mobile devices let workers access short lessons anywhere during breaks, before shifts, or right at the job site. These microlearning sessions focus on one topic at a time and only take a few minutes to complete.
This approach helps workers stay current without taking them off the floor. Whether it's reviewing emergency steps or checking gear procedures, quick refreshers reduce confusion and help people apply training on the spot.
Why mobile learning works:
- Easy access. No need to leave the site to learn.
- Smaller lessons. Focused content improves recall.
- Fits any schedule. Workers can learn when it’s convenient.
- Fewer disruptions. Training doesn’t interrupt daily output.
This format is especially useful for reinforcing high-risk procedures, updating safety rules, or preparing for inspections. It supports a steady learning rhythm without requiring major time blocks.
Data-Driven Feedback and Adaptive Training Paths
Tracking progress is just as important as teaching. Without data, it’s hard to know if training is working. Smart tools now offer detailed feedback based on how workers perform during exercises, simulations, and assessments.
Adaptive systems adjust training paths based on each person’s results. If someone struggles with equipment safety but scores well on evacuation steps, the system offers more focus where needed, which saves time and improves outcomes.
Main features of data-driven training:
- Progress tracking. Know who completed what and how they performed.
- Custom paths. Adjust content based on actual skill gaps.
- Early warning. Spot trends before they lead to problems.
- Better reporting. Managers can show real results to regulators or auditors.
These tools also help build long-term safety culture by showing that learning is continuous, targeted, and part of the daily workflow, not a once-a-year task.
Legal Compliance and Global Standards for Mining Safety Training
Regulatory agencies, both local and international, closely monitor mining operations. Safety training is not just about best practices but a legal requirement. Companies that fail to meet standards face heavy penalties, shutdowns, and long-term reputational harm.
Staying compliant starts with understanding what rules apply and ensuring every training module aligns with them. Programs need to be updated regularly to reflect new laws, industry expectations, and changing site conditions. Good safety training also helps build credibility and trust with inspectors, insurers, and partners.
Staying Ahead of Regulatory Changes
Safety regulations don’t stay the same. Agencies often revise guidelines to reflect new risks, technologies, or incidents in the industry. Companies that ignore these updates fall behind quickly, which can lead to serious legal trouble. Staying compliant means being proactive. This involves monitoring updates from relevant authorities, revising internal training content, and retraining staff when rules shift.
Some changes are minor and can be added to existing lessons. Others require larger overhauls, including new documentation or retraining entire teams. The faster a company responds to these changes, the easier it is to avoid penalties or unsafe conditions. Delays in compliance often lead to unannounced inspections, legal investigations, or operational restrictions.
ISO, MSHA, and Beyond: Which Framework Fits You?
Different countries and industries rely on specific frameworks to regulate safety. In mining, two of the most widely used are ISO standards and MSHA regulations. Choosing the right framework depends on where your site operates, what materials are involved, and the scale of your operations.
MSHA (Mine Safety and Health Administration) sets rules for U.S.-based mines and outlines detailed safety requirements, from equipment procedures to emergency plans. It’s strict, regularly enforced, and designed to reduce coal and metal/nonmetal mining accident rates. Training under MSHA must be documented, role-specific, and updated often. Any site operating in the U.S. needs to meet these rules without exception.
ISO 45001 is a global framework for occupational health and safety management systems. Unlike MSHA, it applies across industries and offers more flexibility. Companies that operate internationally often choose ISO to maintain a consistent approach across borders. It also helps align internal safety programs with supply chain expectations and audits.
Some companies use both, depending on their needs. Others include local standards, mainly when operating in areas with mining-specific rules not covered by ISO or MSHA. The best approach is to identify what rules apply legally and then build a training system that exceeds them. That creates room for better performance, fewer surprises during audits, and safer outcomes overall.
Case Studies: Safety Training That Transformed Operations
Real improvements in mining safety often begin with practical training changes. Abstract strategies don’t matter unless they lead to better outcomes in the field. Case studies show how the right tools and methods can prevent injuries, cut costs, and improve response times. This section focuses on programs that bring measurable, long-term results.
From Tragedy to Turnaround: The Example of a Real-World Solution
A large mining site struggles with repeated chemical handling issues. Near misses, equipment damage, and low confidence among workers raise concerns. Safety briefings feel disconnected from tasks, and staff often skip steps due to unclear instructions. Management brings a focused solution: HAZWOPER/HAZCOM training, created by Humulo.
The program covers chemical safety basics, PPE usage, MSDS interpretation, safe storage, disposal, and real-time incident response. Delivered as a VR experience, the course places workers in a fully interactive chemical handling environment. They move through scenarios where they must identify materials, apply correct gear, and respond to timed challenges based on realistic accidents.
Before advancing, each trainee completes a quiz that tests their understanding of MSDS sheets. The final stage simulates what happens when safety procedures are ignored.
Training is offered in both English and Spanish. Workers access it through supported VR headsets like Meta Quest and Pico Neo models. The 3D design ensures tasks feel familiar and practical, not abstract or forced.
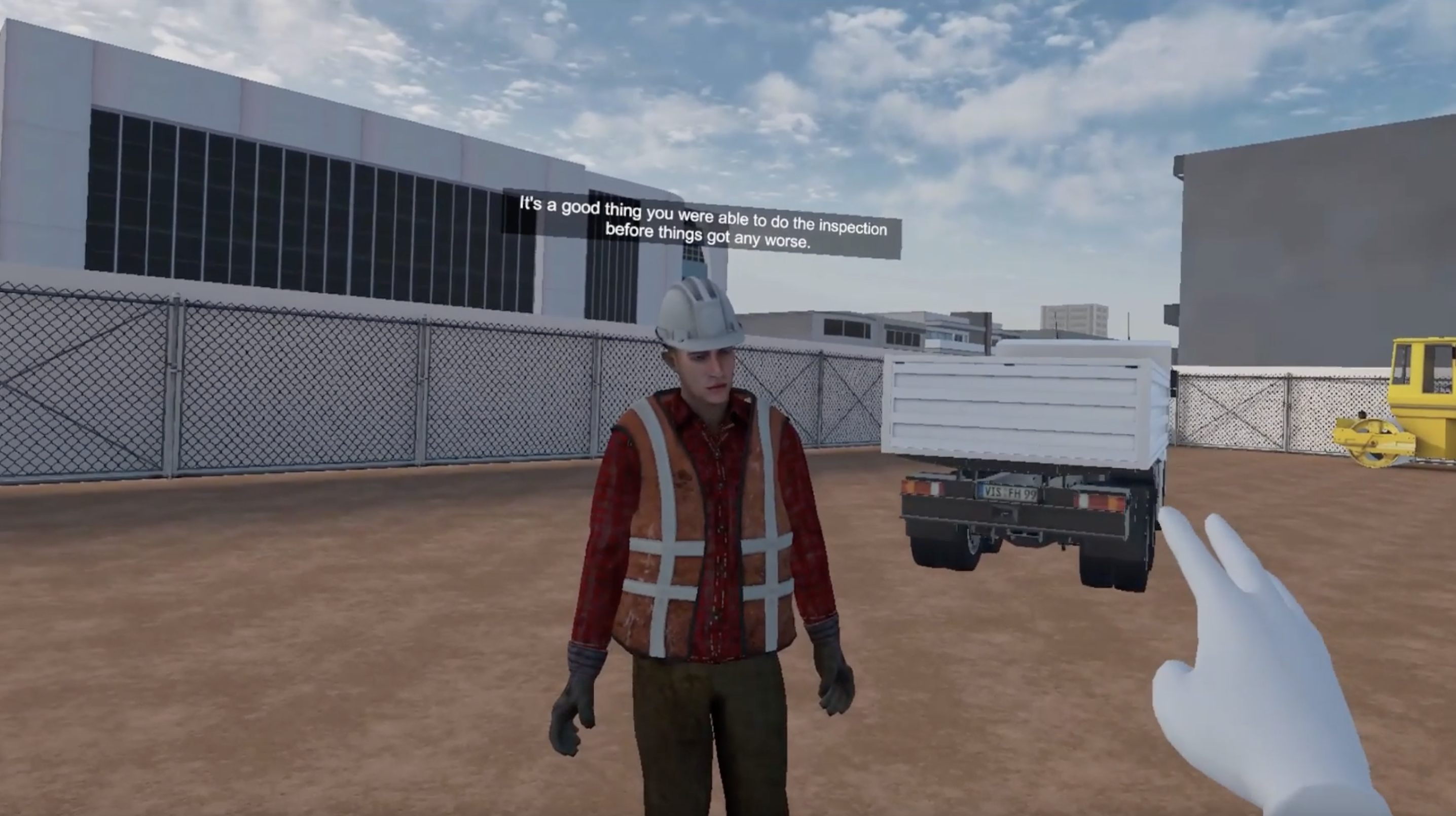
General Hazard Recognition
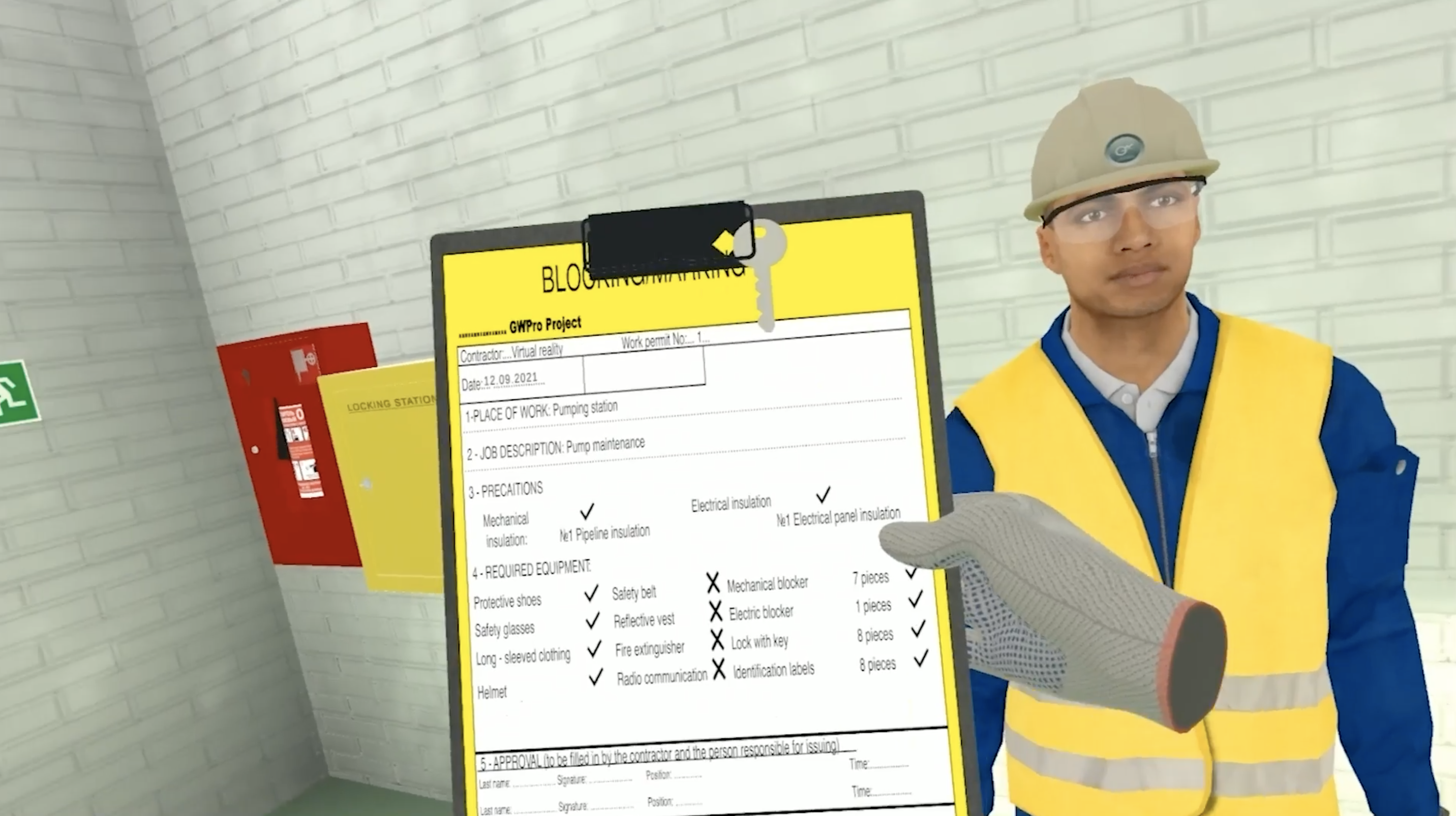
Lockout tagout (LOTO)
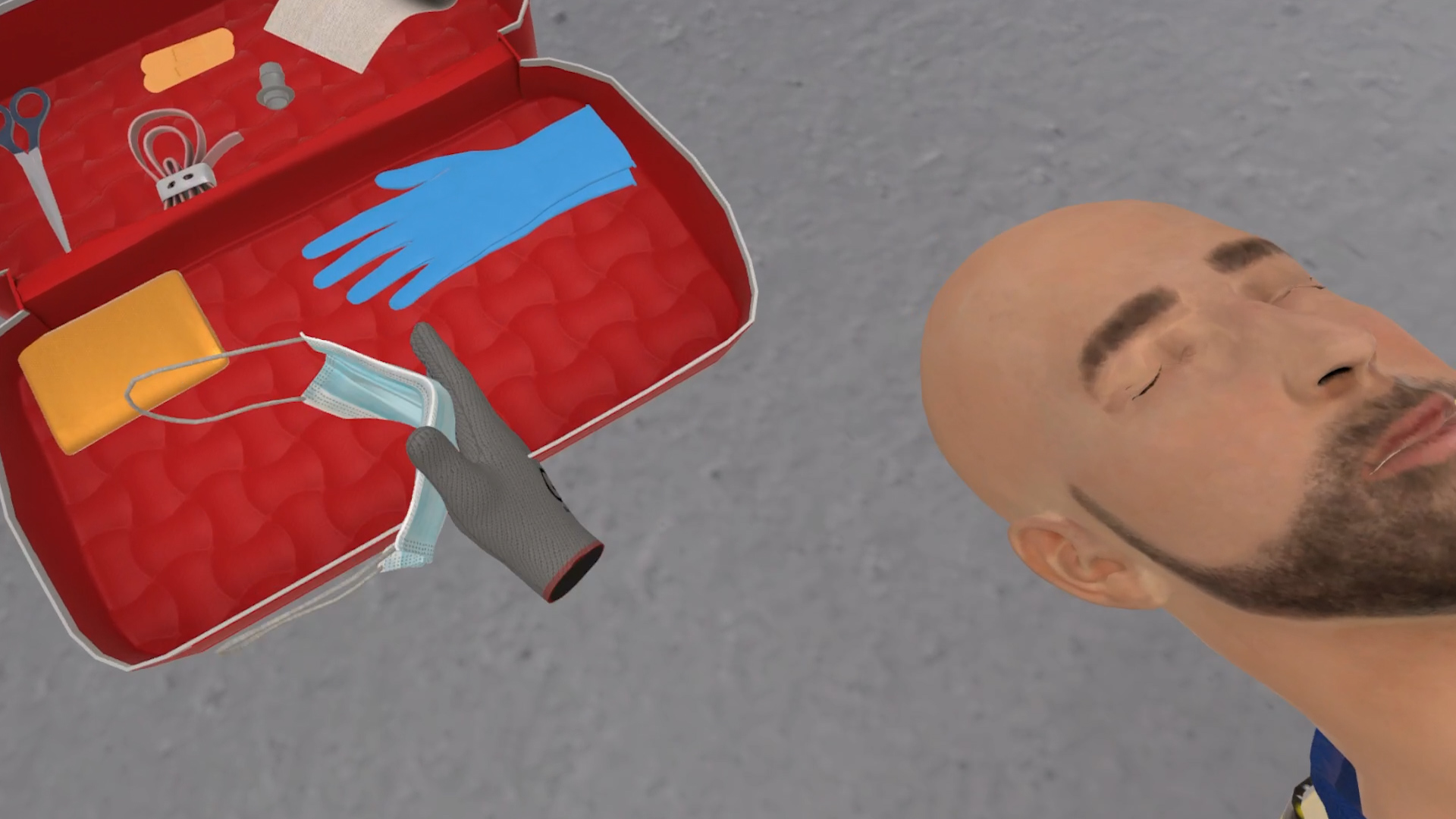
First Aid
Off-the-Shelf Products
Get started fast with our ready-to-use solutions
Benchmarking Safety Performance Post-Training
Training should always produce measurable results. After a program ends, companies must check whether it improves safety outcomes. This means tracking specific metrics — not just general feedback.
Useful benchmarks include a reduction in incident rates, faster emergency response, better compliance during audits, and increased use of PPE. These numbers should be compared before and after training to see what’s working and where more focus is needed.
Managers also reported fewer delays due to unclear protocols. By watching these numbers over time, leadership was able to prove the training had a direct operational impact. Benchmarking also helps with planning future training cycles. Companies can adjust their programs without guessing when they know what improved and what didn’t.
Mining Safety Training ROI: The Numbers Tell a Story
Effective safety training delivers measurable financial value. It reduces operational risks, lowers the frequency of incidents, and ensures regulatory compliance. In the mining sector, even one avoided accident can offset the cost of training for an entire team. The impact is not limited to fewer injuries; it includes reduced downtime, lower insurance premiums, and stronger audit results. The data makes the case clear: a well-structured training program directly supports both safety and financial performance.
Quantifying Risk Reduction and Cost Savings
Accidents in mining lead to significant expenses. These include direct costs such as medical treatment, legal settlements, equipment repair, and indirect losses like halted production and emergency investigations. Safety training helps reduce these risks by preparing workers to identify and avoid hazardous situations before they escalate.
For example, implementing targeted training modules on equipment handling or chemical safety often results in a noticeable drop in incident reports. In some cases, mines have documented a reduction of over 40 percent in reportable safety violations within the first year of structured training. These outcomes lead to fewer fines from regulatory agencies and fewer workdays lost due to injury.
Insurance providers also factor training into their risk assessments. Sites with verified, ongoing safety programs will likely qualify for reduced premiums. Maintenance costs decrease as equipment is handled more carefully, and emergency response costs drop when incidents are managed quickly and correctly.
Productivity Gains and Workforce Morale
Training affects more than compliance and risk. It also improves how people work together. When staff members understand safety procedures clearly, they spend less time second-guessing decisions and focusing more on their tasks. This clarity results in fewer interruptions, smoother operations, and higher productivity.
Workers who feel safe tend to stay longer and show stronger engagement with their work. In environments where safety is prioritized, employee turnover tends to decrease, and collaboration improves. This is especially important in mining, where experienced staff are critical to maintaining workflow and preventing delays.
A well-trained team is more efficient and more confident. With clear processes in place, daily tasks are completed faster and with fewer errors. Time is not wasted correcting mistakes or managing emergencies that could have been avoided. These improvements in performance and morale contribute to a more stable and cost-effective operation.
Building Your Safety Training Roadmap
A strong training program begins with a clear, step-by-step plan. Before investing in new tools or systems, it is essential to understand current gaps, define measurable goals, and select reliable delivery methods. Every decision in the process should be based on the specific needs of the site and the roles involved. A well-structured roadmap ensures that safety training becomes a consistent part of operations, not just a reaction to incidents.
Assessing Needs: Audits and Gap Analyses
Understanding what your workforce needs is the starting point for any effective safety training plan. Assumptions can lead to wasted resources or missed risks, so relying on actual data, formal audits, and feedback from across the organization is important. A structured assessment process ensures the training program is grounded in your site's real conditions and responsibilities.
- Conduct internal safety audits. Review recent incident reports, employee feedback, and inspection outcomes to identify areas of concern.
- Map out role-specific risks. Analyze which positions face the highest exposure to hazards and whether their current training reflects those realities.
- Evaluate current materials. Check if existing training content aligns with regulatory standards and covers all required topics.
- Identify weak points in response readiness. Focus on areas such as emergency evacuation, equipment shutdown procedures, and chemical spill response.
- Use third-party assessments when needed. Independent evaluations can uncover overlooked risks and provide fresh insights.
Accurate assessment is the first step toward building a program that addresses actual operational needs instead of theoretical issues. Our white paper, Immersive Safety and Emergency Training Solutions for High-Risk Workplaces, provides additional guidance on identifying gaps and structuring effective learning for hazardous environments.
Choosing the Right Partners and Platforms
Selecting a training provider or platform is not just about features or pricing. It involves evaluating whether the solution fits your team's distinctive operational, technical, and cultural needs. The right partner will support not only content delivery but also long-term integration and adaptability as your processes and risks evolve.
- Research vendors with relevant experience. Focus on those that have developed safety programs specifically for mining or similarly high-risk industries.
- Evaluate delivery formats. Consider whether classroom, mobile, virtual, or blended formats match your worksite's needs and infrastructure.
- Ensure compatibility with existing systems. Training platforms should integrate smoothly with your current learning management system or tracking software.
- Check for multilingual support. If your workforce includes non-native speakers, language options are essential.
- Review case studies and performance metrics. Only select partners that can demonstrate measurable improvements from their training programs.
- Confirm access to updates and technical support. A reliable vendor offers ongoing assistance and refreshes course content to meet changing standards.
The right partner delivers content and supports implementation and long-term adoption across teams.
Measuring Impact and Continuous Improvement
Training programs must be monitored after implementation to confirm they are producing results. Without tracking outcomes, it is impossible to know whether the program reduces risk, improves behavior, or aligns with safety goals. Ongoing measurement ensures that improvements are not one-time efforts but part of a stable, repeatable system.
- Track performance metrics after training. Monitor incident rates, audit results, and completion records to gauge effectiveness.
- Gather feedback from employees. Ask how confident they feel in applying procedures and whether any content was unclear or missing.
- Use digital tools to analyze data. Platforms with built-in analytics can highlight trends and pinpoint areas for improvement.
- Set benchmarks for success. Define clear targets, such as reducing incidents in specific areas or improving compliance audit scores.
- Schedule regular training reviews. Content should be updated based on real-world results, equipment changes, or regulation shifts.
- Encourage reporting and transparency. A culture of feedback supports faster updates and ensures training stays relevant.
Measuring outcomes is not optional. It is the only way to confirm that training programs are doing their job and helping the site operate safely and efficiently.
Mining Safety Training as a Competitive Edge with Program-Ace
When safety becomes a built-in part of daily routines, workers make faster, smarter decisions, and managers spend less time dealing with preventable disruptions. Program-Ace, as an innovative solutions integrator, offers custom safety training tools designed specifically for high-risk industries like mining.
Our team delivers tailored content using cutting-edge platforms, including VR, mobile, and simulation-based systems. Each solution is built around your team's real conditions on-site, with measurable outcomes and full support for updates and scaling.
If you are looking to improve your training programs and make safety a true operational strength, we’re here to help. Contact us to explore how a customized training strategy can give your operation a lasting competitive edge.