The rise of immersive technologies has opened new possibilities for developing workforce skills in manufacturing. Virtual training solutions, particularly in additive manufacturing training, reshape how employees gain practical knowledge and expertise.
By integrating VR and AR into training programs, businesses provide a safer and more cost-effective way to prepare their teams for complex processes and cutting-edge equipment.
Immersive approaches allow employees to practice tasks in controlled environments, reducing risks and operational downtime. Additive manufacturing training, for instance, benefits significantly from this shift, as workers can learn intricate techniques without the need for expensive materials or prototypes. Through tailored virtual experiences, organizations ensure that their workforce is better prepared to meet modern manufacturing demands.
Virtual training solutions also support continuous learning, enabling teams to keep pace with technological advancements. From machine operation to safety protocols, these tools create engaging and practical training scenarios that improve retention and skill application. As industries face increasing skill gaps, immersive methods play a vital role in enhancing employee readiness and efficiency. With such advancements, immersive technologies are now essential in manufacturing.
The Shift Toward Immersive Manufacturing Training
Manufacturing has increasingly embraced virtual corporate training to enhance workforce skills and improve operational efficiency. Immersive technologies like VR and AR provide workers with hands-on learning opportunities in a controlled digital environment, minimizing risks and reducing costs.
Many organizations are moving away from traditional methods to adopt these solutions due to their ability to simulate real-life manufacturing processes with high precision. By adopting immersive training, businesses ensure employees are prepared to handle complex tasks while staying ahead in an evolving industry.
What Is Immersive Manufacturing Training?
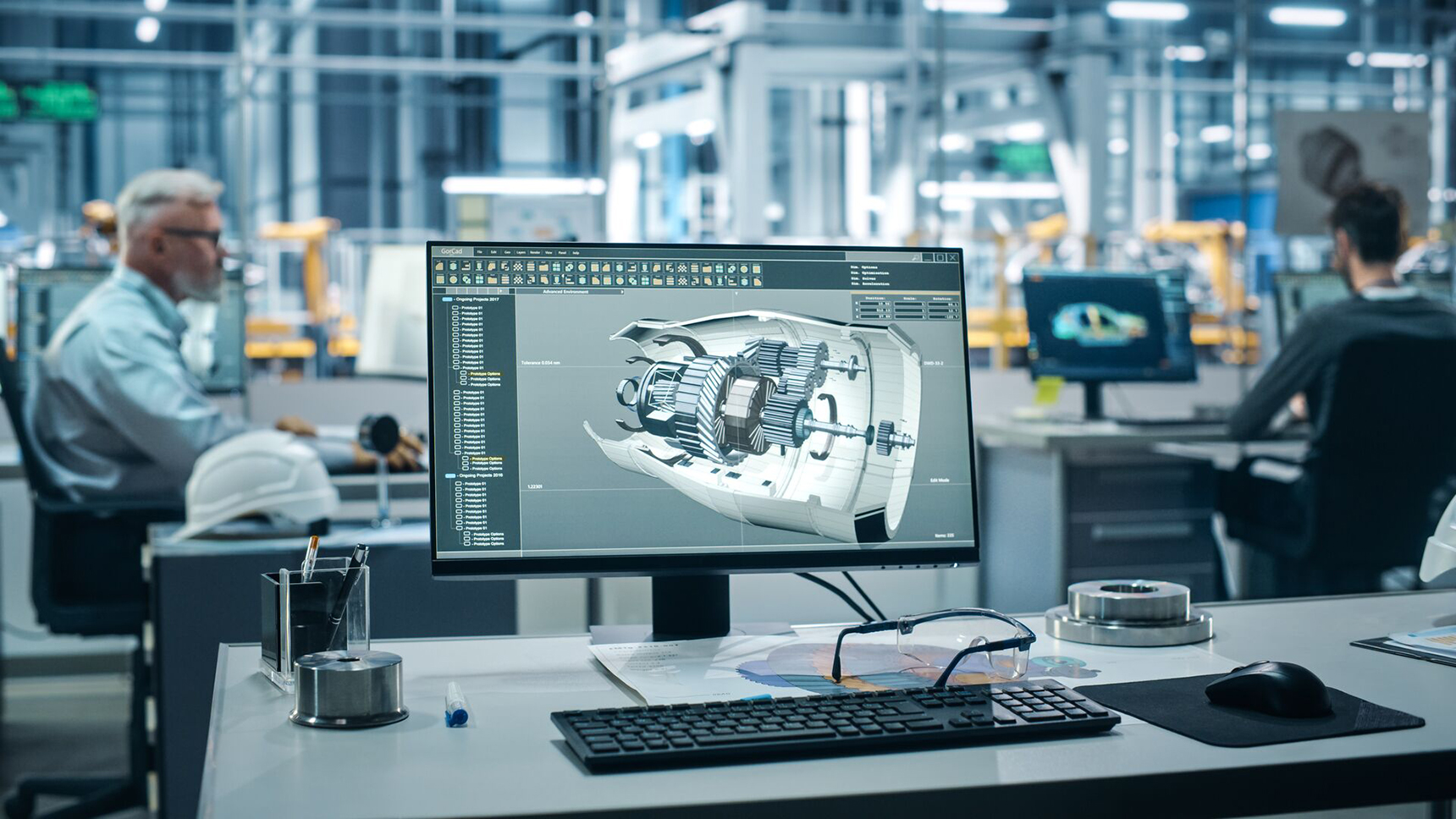
Immersive manufacturing training leverages advanced technologies such as augmented reality in manufacturing to deliver practical learning experiences. Unlike conventional approaches, AR enables workers to interact with virtual models of equipment, assembly lines, or entire factories, fostering better understanding and skill development.
Training programs that incorporate augmented reality in manufacturing allow employees to visualize tasks step-by-step, which improves retention and accuracy in applying new skills.
Using AR, workers can explore scenarios that mirror workplace challenges, such as troubleshooting machinery or following intricate safety protocols. This method enhances preparedness without disrupting production schedules or incurring material waste.
Such tailored training solutions also adapt to varying skill levels, ensuring both new hires and experienced personnel receive relevant, effective guidance. By prioritizing immersive tools, industries elevate workforce capabilities to meet modern demands.
Benefits of VR/AR in Manufacturing Training Programs
Virtual reality and augmented reality have introduced numerous advantages in training manufacturing processes, significantly enhancing workforce readiness. The integration of VR and AR ensures practical and effective learning environments tailored to real-world challenges. Key benefits include:
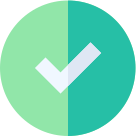
Improved safety compliance. Employees can practice dangerous tasks in a virtual setting, minimizing risks during the learning phase.
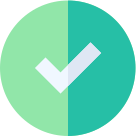
Enhanced retention rates. Interactive and immersive methods help workers retain information more effectively than traditional training.
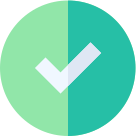
Reduced downtime. Training in VR or AR allows employees to gain hands-on experience without interrupting ongoing operations.
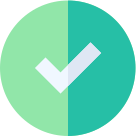
Cost efficiency. Virtual scenarios replace physical prototypes or setups, significantly reducing training expenses.
Adopting VR and AR in manufacturing training extends beyond improving individual skills. It transforms the entire learning approach into a scalable, efficient process that meets the industry’s most pressing demands. Companies implementing these solutions often see faster workforce readiness and better adaptability to new technologies, creating a competitive advantage.
Trends Driving the Rise of VR/AR Manufacturing Training
The growing need for adaptable and efficient workforce training has amplified the demand for VR training solutions across various industries. In manufacturing, specific trends highlight why immersive methods are gaining traction:
- Integration of VR soft skills training. Managers and supervisors use VR scenarios to develop leadership and decision-making capabilities.
- Adoption in high-risk sectors. VR training solutions for oil and gas demonstrate how immersive tools provide safe, realistic simulations for handling hazardous materials or environments.
- Alignment with digital transformation. Companies leverage VR/AR to meet Industry 4.0 requirements, ensuring employees can operate advanced machinery and systems.
- Customization and scalability. Virtual training platforms offer tailored content that adapts to different job roles, making training scalable for large teams.
The popularity of immersive training reflects a significant shift in how industries approach workforce development. Beyond simply meeting training goals, VR/AR fosters adaptability and resilience, equipping employees to succeed in rapidly evolving environments. Organizations leveraging these trends position themselves for sustainable growth in an increasingly competitive manufacturing landscape.
Key Types of Immersive Manufacturing Training Programs
Immersive training programs are tailored to meet the diverse needs of the manufacturing industry. Different types of simulation training ensure practical knowledge transfer for workers at every level.
- Safety simulations. Employees learn to handle emergencies and follow safety protocols without exposing themselves to real-world risks.
- Process optimization training. Workers practice and refine manufacturing tasks in a virtual environment to increase efficiency and precision.
- Soft skills development. Supervisors improve leadership and communication skills using immersive role-playing scenarios.
Manufacturing sectors rely on various VR/AR simulations to provide targeted solutions for complex challenges. The flexibility and effectiveness of these programs allow organizations to design comprehensive training strategies for both technical and interpersonal growth. Immersive methods are becoming indispensable tools in modern training practices by covering a wide range of needs.
Manufacturing Safety Training — Ensuring a Secure Workplace
Workplace safety remains a cornerstone of effective manufacturing operations. Manufacturing safety training using immersive technologies like VR and AR enables employees to handle risks confidently and precisely. Virtual environments allow workers to practice safety procedures without real-world consequences, ensuring they are fully prepared for potential hazards.
Emergency evacuation simulators play a significant role in this approach. Employees rehearse evacuation protocols for fires, chemical leaks, and other emergencies, learning to respond quickly and effectively under pressure. These simulations improve individual readiness and refine team coordination during high-stakes scenarios.
In addition to evacuation training, immersive tools teach employees to manage hazardous materials safely, operate heavy machinery, and identify workplace hazards. Simulated environments mirror the specific conditions of a facility, offering tailored safety scenarios that address the unique risks of each workplace.
Organizations adopting immersive manufacturing safety training report reduced workplace accidents and enhanced compliance with safety regulations. Workers gain a deeper understanding of safety protocols, fostering a proactive safety culture across the organization. By integrating VR and AR into their training programs, manufacturers protect their employees and achieve operational continuity, avoiding disruptions caused by accidents or regulatory issues.
Training Manufacturing Processes with VR/AR Simulations
Mastering manufacturing processes requires practical experience, and VR/AR simulations offer an efficient way to provide it. Tools like the oil platform simulator deliver hands-on training without risks or production downtime, enabling employees to gain confidence and proficiency. Key areas of focus include:
- Precision assembly. Workers practice assembling intricate components, ensuring accuracy without wasting materials.
- Machinery operation. Simulations teach employees how to operate complex machinery, reducing the likelihood of errors.
- Process optimization. Trainees identify inefficiencies in workflows and test improvements in a virtual environment.
- Troubleshooting skills. Workers learn to detect and resolve equipment malfunctions in simulated scenarios, improving problem-solving abilities.
- Maintenance training. Employees practice preventive and corrective maintenance techniques on virtual equipment, minimizing the risk of real-life damage.
Immersive training tools help organizations deliver process-specific skills efficiently and effectively. With VR/AR, employees receive targeted guidance, enabling them to refine their expertise while avoiding disruptions to production. Businesses adopting these solutions report improved performance and reduced training costs, making simulations integral to modern manufacturing operations.
Leadership Training for Manufacturing Supervisors
Supervisors in manufacturing play a crucial role in bridging technical operations and team management. Immersive leadership training programs combine practical applications, such as manufacturing sales training, with interpersonal development tools. Through VR, supervisors engage in real-life scenarios, learning to lead teams under high-pressure conditions while maintaining productivity and morale.
Unlike traditional methods, immersive training integrates specific challenges manufacturing supervisors face, such as managing technicians with varying expertise or meeting customer demands. Manufacturing technician training included in these programs ensures leaders understand technical workflows, fostering collaboration and respect within teams. Additionally, VR-based sales training equips supervisors with skills to align production outcomes with market demands.
This multidimensional approach helps manufacturing supervisors grow into well-rounded leaders capable of driving efficiency while ensuring their teams remain motivated and aligned with organizational goals. Immersive tools redefine leadership training, blending interpersonal and technical skills into a seamless learning experience tailored to industry needs.
The Role of Immersive Tech in Addressing Manufacturing Challenges
Immersive technologies are reshaping how manufacturing challenges are addressed, offering solutions that improve workforce readiness and operational efficiency. Manufacturing training software built on VR and AR platforms creates environments where employees can master essential skills without disrupting production. These tools provide practical learning opportunities while reducing costs, improving safety, and addressing workforce gaps.
Bridging Skill Gaps in the Manufacturing Workforce
Skill gaps remain a pressing issue in manufacturing, particularly in sectors requiring advanced expertise. VR training solutions for oil and gas provide a clear example of how immersive tools address this problem by offering hands-on, realistic scenarios tailored to industry needs. Workers gain experience handling specialized tasks, such as operating complex equipment, without risking real-world consequences.
These immersive solutions extend to broader manufacturing applications, enabling workers to learn or refine new skills more efficiently. Employees gain confidence in their abilities by replicating challenging operational environments, such as high-pressure scenarios or intricate production processes. This approach minimizes on-the-job errors, reduces learning curves, and accelerates workforce readiness.
Manufacturers using VR training solutions consistently report improved worker performance, adaptability, and productivity. By providing scalable and customizable programs, immersive tools ensure organizations can effectively address diverse training requirements. This shift prepares employees for specific roles and contributes to a more versatile and capable workforce.
Enhancing Retention and Knowledge Transfer in Manufacturing
Retaining critical knowledge and ensuring its transfer across the workforce are ongoing challenges in manufacturing. Leadership training for manufacturing supervisors using immersive technologies focuses on delivering impactful learning experiences. Supervisors practice communication, decision-making, and problem-solving in realistic scenarios that improve engagement and understanding.
Virtual training environments cater to various learning styles, allowing employees to interact directly with content. Immersive tools, such as VR simulations, transform abstract concepts into tangible experiences. This method reinforces memory retention, enabling workers to recall and apply knowledge more effectively.
Supervisors also benefit from VR-based leadership training by developing their ability to mentor team members and share expertise. Tailored programs address specific manufacturing needs, ensuring leaders possess the skills to drive performance and operational success.
Adopting immersive solutions boosts long-term organizational knowledge while creating a more capable and cohesive team. Workers feel more confident in applying what they learn, and supervisors are better equipped to cultivate a culture of continuous improvement across manufacturing operations.
Adapting to Rapidly Changing Manufacturing Technologies
The pace of digital transformation in manufacturing demands continuous upskilling to keep employees aligned with new technologies and workflows. Immersive training solutions like VR and AR address this need by providing scalable and adaptable methods for teaching cutting-edge processes and tools.
- Streamlined onboarding. New hires familiarize themselves with equipment and workflows through interactive simulations, reducing training time.
- Hands-on learning for advanced tools. Workers gain practical experience with emerging technologies without requiring access to expensive machinery.
- Scenario-based troubleshooting. Employees learn to identify and resolve technical challenges in virtual environments, building confidence for real-world situations.
- Ongoing skill enhancement. Immersive programs ensure workers stay updated on the latest industry developments, supporting continuous professional growth.
Immersive training tools empower workers to adapt to rapidly changing demands while minimizing operational disruptions. As manufacturing technologies evolve, VR and AR serve as essential components of workforce development, enabling companies to stay competitive and meet dynamic industry needs.
Empower your workforce with a top-notch manufacturing training program.
Building Effective Manufacturing Training Programs with VR/AR
Creating impactful manufacturing training programs requires aligning immersive technologies with the organization’s operational goals. VR/AR-based solutions offer customizable training content tailored to specific processes and challenges, ensuring employees develop practical and transferable skills.
Designing an Engaging and Realistic Training Environment
Effective training environments must replicate real-world conditions to maximize learning outcomes. Virtual and augmented reality provide the tools necessary to create realistic, interactive scenarios that engage trainees and improve skill retention.
- Accurate simulation of tasks. Trainees experience lifelike representations of manufacturing processes, allowing them to practice skills in a controlled setting.
- Dynamic feedback mechanisms. Immersive environments provide real-time feedback, helping workers refine their techniques and reduce errors.
- Customizable scenarios. Training modules can be tailored to specific roles, from equipment operation to safety protocols, ensuring relevance for all employees.
- Collaborative learning opportunities. Workers can engage in team-based exercises, improving communication and coordination within manufacturing teams.
By designing environments that reflect operational realities, immersive programs foster practical knowledge and prepare employees to meet workplace challenges effectively. Combining accuracy, engagement, and adaptability, these tools create training experiences that drive productivity and operational excellence.
Measuring Success and ROI in Immersive Manufacturing Training
Evaluating the effectiveness of immersive manufacturing training requires a structured approach to measure both qualitative and quantitative outcomes. Clear metrics ensure organizations can track progress and validate the return on investment (ROI) for VR/AR programs.
- Skill improvement metrics. Assessments before and after training sessions provide insights into employee skill enhancement and learning retention.
- Reduced operational risks. Tracking incidents and near-misses, post-training demonstrates the impact of safety-focused immersive programs.
- Time-to-proficiency rates. Monitoring how quickly new hires become productive highlights the efficiency of VR/AR onboarding processes.
- Employee engagement levels. Feedback surveys gauge how immersive programs resonate with participants, ensuring training remains engaging and effective.
- Cost savings analysis. Comparing traditional training costs with immersive program expenses, including material waste and downtime reductions, clarifies ROI.
Organizations implementing measurable outcomes in immersive training programs find greater clarity in evaluating success. Beyond financial returns, workforce preparedness and operational efficiency improvements underscore the value of VR/AR as a long-term investment.
Overcoming Common Barriers in VR/AR Manufacturing Training
The adoption of VR/AR in manufacturing training often encounters several challenges that require practical solutions. High upfront costs remain a common concern for many organizations, yet the potential for long-term savings through reduced material usage and operational downtime outweighs these expenses. Clear communication about the benefits of immersive training can also help address resistance among employees, especially when combined with hands-on demonstrations to build familiarity and trust.
Technical limitations, such as hardware compatibility or software scalability, need careful planning during the initial stages of implementation. Regular updates and the selection of adaptable platforms ensure that training solutions remain effective over time. Programs designed to cater to varying skill levels can alleviate difficulties for both new hires and seasoned employees, making the learning process more inclusive and effective.
Limited in-house expertise can also pose a challenge for organizations entering the immersive training space. Collaborating with experienced VR/AR developers provides essential technical and strategic support, ensuring smooth program execution. By preparing thoroughly and addressing these challenges, organizations can unlock the full potential of immersive training and create a workforce equipped to meet modern manufacturing demands with confidence and efficiency.
Manufacturing Training Examples to Learn from
Immersive technologies are transforming manufacturing training, with real-world applications demonstrating their effectiveness. Two noteworthy examples, the Emergency Evacuation Simulator, and the Oil Platform Simulator, illustrate the value of these solutions in addressing unique challenges.
Emergency Evacuation Simulator
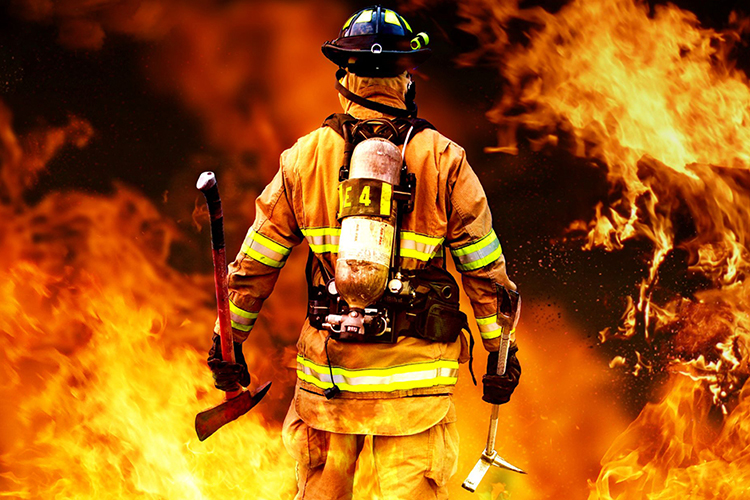
The Emergency Evacuation Simulator, designed for a U.S.-based construction client, prepared office employees for emergencies in a five-story building. Key features included a voice communication module, health status indicators, and centralized rating systems for assessing progress. This solution helped train over 2,000 employees and reduced emergency evacuation incidents by 44%.
Oil Platform Simulator
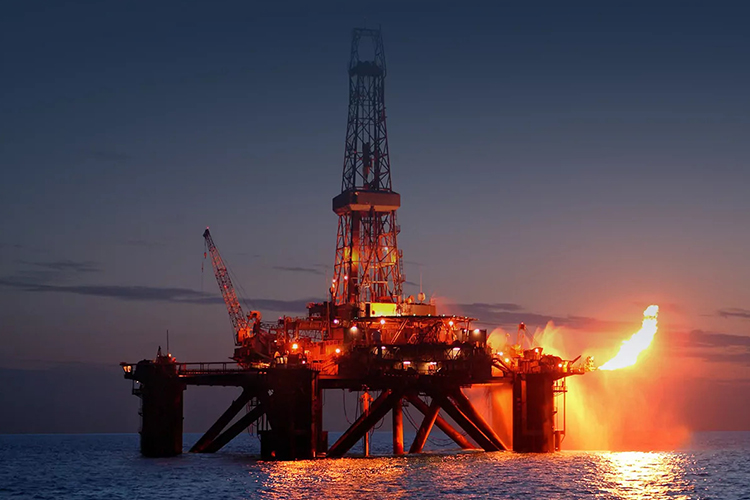
The Oil Platform Simulator, built for the oil and gas industry, offered a comprehensive training tool for offshore platform employees. This simulator covered daily operations, emergency evacuations, and process optimization. Its customizable environment allowed real-time simulations, bot interactions, and scenario planning, reducing workplace accidents by 43% and improving equipment adoption times by 27%.
Both simulators highlight the practicality of immersive manufacturing training. These examples demonstrate how VR/AR technologies improve safety, streamline learning, and deliver measurable results in diverse industries, setting benchmarks for effective training solutions.
The Expanding Role of Immersive Technology in Global Manufacturing
Immersive technology continues to reshape manufacturing, offering scalable solutions for skill development, safety improvement, and process optimization. Manufacturing software development services utilizing VR and AR empower businesses to adopt efficient training methods and innovative operational strategies.
With immersive tools, manufacturers simulate complex tasks, allowing employees to practice in realistic virtual environments. These applications improve knowledge retention, reduce errors, and enhance readiness for emergencies or new processes. For example, VR-based simulations enable workers to safely engage with hazardous tasks, such as equipment operation or chemical handling, without real-world risks.
Another area where immersive technology excels is customization. Manufacturers benefit from solutions tailored to their unique processes, facilities, and objectives. From assembly line training to leadership development, immersive software adapts to diverse industry needs. Analytics modules further enhance these programs, providing data to assess employee performance and refine training approaches.
The adoption of manufacturing software development services with immersive technology is no longer optional; it has become a key driver of operational excellence in global industries. Businesses leveraging VR and AR ensure their workforce stays competitive while maintaining high standards for safety and efficiency.
Why Program-Ace Is Your Trusted Partner for VR/AR Manufacturing Training Programs
Program-Ace has a proven track record as an innovative solutions integrator, offering expertise in immersive technology for manufacturing. Our manufacturing training programs deliver practical, tailored results that enhance workforce skills and ensure alignment with industry requirements.
Our approach includes end-to-end manufacturing software development services, combining advanced VR/AR tools with user-friendly designs. These solutions are adaptable, ensuring they meet the unique demands of each client’s operations. Program-Ace also excels in integrating analytics and customization features to make training measurable and scalable.
Ready to take your training to the next level? Contact us today to explore how our solutions can transform your workforce development strategies and ensure long-term success.