There is no denying that technological innovation is moving faster now than ever before, and getting on board with the changes is the mark of a successful business. At first glance, manufacturing might not seem like an industry that requires much change: after all, we have been mass-producing things for over a century and have become pretty damn good at it. However, manufacturing software development, machine learning, and other forms of digital transformation have the potential to boost the evolution of the industry even further.
Digital transformation in manufacturing is what we call the use of digital technologies for the betterment of manufacturing processes: from the very first stages of planning to the end results of production. It can boost manufacturing efficiency, quality, and accessibility with a range of solutions of different scope. For example, it could be a single app used by a production supervisor or an entire software ecosystem integrated into each business process.
To get a better grasp of the phenomenon and what it can do for businesses, let’s explore the topic more thoroughly.
Looking for digital transformation services? Don't hesitate to speak with us!
The Importance of Data Analytics in Digital Transformation
Data analytics plays a critical role in digital transformation within the manufacturing sector. Manufacturers can gain insights into operational performance, customer behavior, and market trends by utilizing data collected from various processes. Such a data-driven approach enables companies to make informed decisions, streamline operations, and identify areas for improvement. For instance, predictive analytics can help anticipate equipment failures before they occur, allowing for proactive maintenance and minimizing downtime.
Moreover, data analytics tools facilitate real-time monitoring, enabling manufacturers to track key performance indicators (KPIs) and assess the efficiency of their production lines. This immediate feedback loop empowers teams to respond quickly to anomalies, optimizing productivity and resource allocation.
By integrating analytics into their workflows, manufacturers enhance their decision-making capabilities and foster a culture of continuous improvement. The ability to adapt to changing conditions and demands is crucial in today's competitive landscape. Ultimately, data analytics is an indispensable component of digital transformation, driving growth and innovation throughout manufacturing.
Types of Transformative Solutions
Digitizing your business does not simply mean setting up computers and running a certain program: the variety of solutions in this field is vast, and some of the main types include:
3D product visualization
For product-oriented companies, product visualization offers several internal and external benefits. It typically involves an interface that displays a rendered product model with interactive options like rotation, color modification, and zoom, allowing users to explore the product in detail. With the help of such solutions, you can offer another realm to your product.
In some cases, a complete product configurator is developed, enabling users to customize the product to their specific preferences, which enhances their understanding and engagement. Internally, these visualizations are highly useful for company staff, as they assist in future product development by offering detailed models that can be analyzed and modified. Such an approach helps identify potential improvements and make informed decisions. Additionally, visualizations can boost operational efficiency, as teams can collaborate better using explicit 3D representations of products.
For instance, these models can be integrated into a PLM (product lifecycle management) system, optimizing various stages of a product's lifecycle, from material acquisition to distribution. Externally, product visualization is beneficial for presenting products to customers in a more accessible and engaging manner, ultimately improving the shopping experience and increasing the likelihood of conversions.
Training and simulation
Some individuals in the industry hold the belief that the only effective way to train workers and prepare them for various scenarios that may arise during production is to put them directly in the driver’s seat of the equipment. According to this perspective, hands-on experience with real machinery is the most effective way for workers to acquire the necessary skills.
While practical, this method comes with significant drawbacks. It is rarely the safest approach, as inexperienced workers may inadvertently cause accidents or equipment damage. Moreover, this can disrupt the overall operation of the facility, potentially resulting in production delays and increased costs.
Fortunately, advancements in modern technology have given us far safer alternatives while still providing a similar level of practical knowledge. Digital training programs and simulations can replicate real-life working conditions without any associated risks. For instance, workers can participate in training programs where they control a virtual avatar that operates heavy machinery.
Through this immersive experience, trainees can observe and practice the necessary movements and procedures involved in using the equipment while avoiding the dangers associated with direct interaction. Furthermore, workers do not need to be physically present near the equipment, allowing for a more flexible and accessible training process.
Digital twins
Digital twins are virtual representations of real-life objects, systems, and processes. One of their key traits is their high level of accuracy, as they are typically created using real physical data and precise measurements. For instance, a digital twin of a pump might involve attaching several sensors that measure parameters such as water flow, pressure levels, and other relevant data points.
These sensors provide continuous, real-time information that ensures the digital twin mirrors the physical pump as accurately as possible, making it a reliable representation. Creating a digital twin of this kind can provide businesses with numerous benefits. It allows companies to prototype changes to their existing products or develop entirely new models more effectively by simulating real-world conditions and responses without having to build a physical prototype.
This saves time and significantly reduces the cost associated with the research and development process. Additionally, digital twins can detect issues with the performance of machinery or integrated systems, allowing for early identification of faults and ensuring that potential problems can be addressed before they escalate. Businesses can also find ways to optimize their processes and improve overall efficiency by analyzing the data collected from the digital twin.
VR/AR development
Virtual and augmented reality have a wide range of uses in manufacturing, mainly due to their ability to create immersive experiences and effectively replicate real environments and physical objects. These technologies provide manufacturers with powerful tools that can be applied throughout the entire production lifecycle. AR/VR allow teams to explore, test, and validate ideas before making physical changes.
By offering realistic visualizations and interactive environments, virtual and augmented reality allow teams to explore, test, and validate ideas before making physical changes, minimizing errors and improving efficiency.
In the context of factories and plants, virtual and augmented reality are invaluable from the very beginning of building planning. For example, AR and VR can be used to visualize a plant layout, enabling stakeholders to walk through the virtual environment and identify potential design issues or opportunities for optimization, allowing for informed decision-making and leading to better utilization of space and resources.
As the project progresses, these technologies continue to be beneficial during equipment installation and setup, providing instructions and support through visual overlays, which helps technicians ensure that machinery is correctly positioned and operational. When designing new product models or preparing for equipment maintenance, wearing AR glasses or a VR headset significantly simplifies the process for workers.
Using these devices, employees can visualize complex models, test their designs in a simulated environment, and make real-time adjustments. The hardware also plays a crucial role in training and skill development, allowing workers to interact with virtual versions of existing equipment and products.
Through these interactions, they can learn how to operate and maintain machinery properly, identify potential issues, and explore areas for improvement without any associated risks or disruptions to production. Ultimately, the use of virtual and augmented reality not only enhances productivity but also contributes to a safer and more informed working environment.
Gamification
Working at a plant might not be everyone’s idea of having fun, but that doesn’t mean the work has to be dull or monotonous. By incorporating gamification, which means adding game-like elements to a learning or work setting, companies can make certain tasks more enjoyable and engaging for their workers. This is one of multiple ways to make the training and working more enjoyable.
Gamification can be applied to various aspects of plant work, making routine activities feel more rewarding. For example, by introducing challenges, achievements, and a points system, companies can incentivize workers to perform their best. Someone working on a production line could log their daily performance metrics through a mobile app, tracking factors like speed, quality, and efficiency.
Based on their results, they could earn points, progress through levels, and receive rewards such as bonuses or recognition from the company. These incentives not only make the work more engaging but also create a sense of competition and accomplishment, making the position more appealing.
In addition to individual rewards, gamification development services can be used to foster teamwork and collaboration among plant employees. Group challenges, such as achieving a collective production target, can encourage workers to communicate and support one another, strengthening team dynamics. As a result, incorporating gamification elements into plant work can significantly change how employees perceive their jobs, transforming potentially tedious tasks into more interactive and enjoyable experiences.
Cybersecurity Considerations in Digital Manufacturing
As manufacturing businesses increasingly adopt digital technologies, the importance of cybersecurity cannot be overstated. Protecting sensitive data and maintaining operational integrity is crucial in an era where cyber threats are becoming more sophisticated. With the integration of connected devices, the risk of cyberattacks increases, making it essential for manufacturers to implement robust cybersecurity measures.
Manufacturers should prioritize the security of their digital infrastructure by conducting regular risk assessments and employing comprehensive security protocols. This includes firewalls, encryption, and intrusion detection systems to safeguard sensitive information from unauthorized access. Also, training employees on cybersecurity best practices is vital, as human error often remains a significant vulnerability.
Furthermore, manufacturers must ensure compliance with industry regulations and standards related to data protection. Establishing a culture of security awareness within the organization helps mitigate risks and fosters a proactive approach to cybersecurity. By taking these precautions, businesses can confidently embrace digital transformation while minimizing the potential for costly security breaches that could disrupt operations and harm their reputation.
Should You Outsource This Service or Keep it In-house?
If you are attracted to the benefits of digital transformation in manufacturing and have decided to modernize your business using a digital approach, you may soon realize that the process is more challenging than initially expected. Implementing these changes internally requires a thorough understanding of well-established strategies within this field and carefully selecting the approach that best aligns with your specific needs and business objectives.
You will also need solid knowledge of the technology stack you decide to use, understanding how it can improve your business operations, and what benefits it can bring. As most digital transformations rely heavily on specialized software, it becomes necessary to assemble a capable team that includes skilled software developers, designers, business analysts, and other specialists to carry out the plan effectively and ensure that each aspect of the transformation is managed efficiently.
Choosing to hire experienced experts in digitization can save you a significant amount of effort and prevent many of the difficulties that often arise from managing such a transformation on your own. Working with professionals with proven expertise in this field provides access to practical knowledge that can be applied directly to your project. This can ensure a much smoother process and prevent common pitfalls.
A trustworthy firm will not only have experience in executing similar projects but will also provide talented software developers, business analysts, and other specialists capable of addressing your business’s unique challenges. With a dedicated team, you can successfully adopt new technologies, enhance your operations, and focus on your core business activities while they handle the complexities of digitization.
Transformative Solutions from Program-Ace
Program-Ace is a company ready to cater to a wide range of transformative needs. This includes all 5 types of solutions listed above as well as others, including certain aspects of machine learning. Below are some of our digital transformation examples in manufacturing:
This is a training application accessible to many users at once. It simulates a situation when workers must quickly escape from a facility due to a fire or other emergency situations.
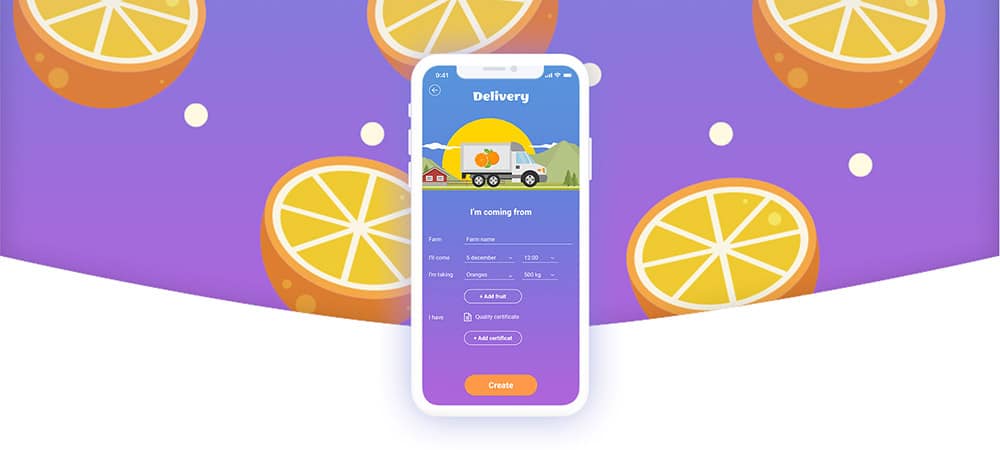
A gamification strategy is implemented in this app. It is meant to be used by both farmers and distributors of goods to make their cooperation more entertaining and meaningful.
Using a wide range of technologies (MR, ML, Cloud, Drones), this platform helps survey farmland, collect data, and identify issues when they occur. While the app is not directly linked to manufacturing, the same scouting and big data solution can be applied in an industrial setting.
The Oil Platform Simulator is another training program built for the benefit of employees. It models a platform where oil is collected and teaches workers how to handle the equipment on the platform, similar to the kind of work done in factories and plants.
Transform Your Manufacturing Power with Program-Ace
Transform your manufacturing capabilities with Program-Ace, an experienced custom software development company dedicated to driving your business forward. Our team specializes in delivering tailored digital transformation solutions designed specifically for the unique challenges of the manufacturing industry. Whether you need advanced software for production management, workforce training, or data analysis, our innovative approach ensures your business remains competitive and efficient in today's fast-evolving market.
By leveraging cutting-edge technologies like augmented reality, digital twins, and machine learning, we help manufacturers optimize every aspect of their operations, from design and prototyping to production and quality assurance. Our expertise allows us to develop custom solutions that perfectly align with your business needs, streamlining processes and enhancing productivity.
Ready to boost your manufacturing potential? Contact us to discuss how our tailored software solutions can help you stay ahead in the industry.