We uncover the main points you should know about DT usage in construction and the value you can harness from it.
Digital twin technology is increasingly integral in various sectors, notably impacting the construction industry. Initially, construction was slower to adopt digital twins construction technology, but it has become one of the primary fields benefiting from this innovation.
Inherent complexities, unique risks, and the need for intricate coordination among numerous stakeholders characterize construction projects. The introduction of digital twins has significantly transformed how these challenges are addressed, enhancing the efficiency of construction firms and contractors. By implementing digital twins in construction, the industry sees improved process streamlining, better stakeholder communication, and effective risk management.
As a specialized digital twin development company, we highlight the substantial benefits and applications of digital twin technology in the construction sector. Digital twins in construction act as dynamic, virtual models of physical assets, enabling professionals to simulate and analyze scenarios virtually before implementation. This use of digital twin construction technology leads to optimized processes, cost reductions, and an elevated level of operational excellence.
Moreover, digital twin technology is instrumental in project planning, execution, and ongoing maintenance. The real-time data and predictive analytics provided by digital twins are crucial for anticipating and mitigating potential issues, thus avoiding expensive downtimes and improving long-term asset management.
So, integrating digital twins construction technology into construction practices is a game-changer, offering enhanced project management, risk mitigation, and cost efficiency. This technology revolutionizes construction methodologies, leading to more accurate, safe, and sustainable projects.
What Is a Digital Twin in Construction?
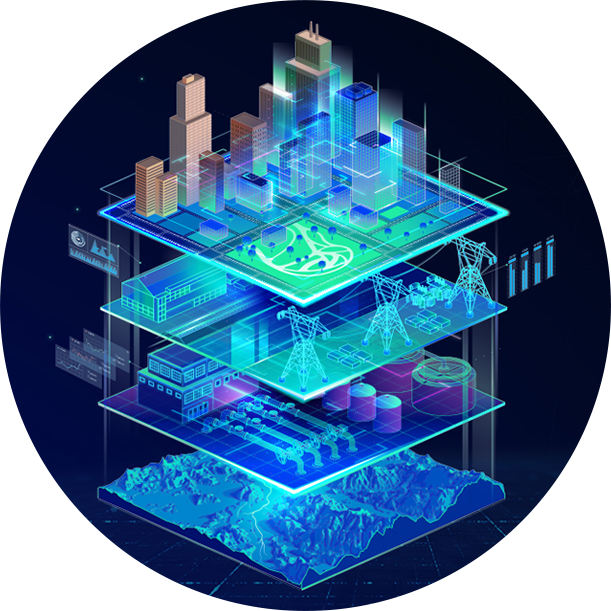
Digital twin technology, characterized as virtual replicas of physical entities that are continually updated in real-time, has become a cornerstone of modern technological advancements. The key feature distinguishing a digital twin from a simulation or a simple virtual copy is its ongoing data linkage. This connection between the physical object and its digital counterpart enables dynamic monitoring, allowing real-time tracking of the object's condition and performance. This capability not only enhances operational efficiency but also paves the way for exploring various what-if scenarios, significantly contributing to the development of the metaverse.
Today the use of digital twins is gaining momentum. For instance, digital twins in manufacturing have demonstrated their efficacy by orchestrating operations within factory environments. Here, they serve as pivotal tools in streamlining production processes, enhancing quality control, and facilitating predictive maintenance. Similarly, the growth of digital twins in healthcare is notable, as they provide clinicians with advanced tools to improve medical care quality. Healthcare professionals can simulate and analyze medical conditions and treatments with unprecedented precision and accuracy through these digital replicas.
The role of digital twins in construction is particularly transformative. A construction digital twin, whether modeling a single building, a group of buildings, a highway, a bridge, or an entire city, offers a comprehensive virtual representation of the project. Typically visualized through sophisticated 3D modeling or augmented and virtual reality solutions, these digital twins in construction allow stakeholders to assess and interact with the space virtually. This interaction is not merely about visual representation; it encompasses many data points — structural details, material properties, and environmental factors — converging within the digital twin building technology to provide a holistic view of the construction project.
Digital twin technology in construction goes beyond visualization; it is about creating a responsive, interactive model that evolves alongside the physical structure. This technology enables construction professionals to preemptively identify potential issues, optimize designs, and improve decision-making processes. Using digital twin building technology, construction projects become more efficient, cost-effective, and sustainable. Implementing digital twins in construction projects signifies a shift towards more intelligent and adaptive construction practices.
As a result, integrating digital twin technology across various sectors, including manufacturing, healthcare, and construction, has opened new frontiers in operational efficiency and innovation. These digital twins, far from static models, are dynamic entities that evolve in real time, offering unprecedented interaction and insight into physical objects and systems. As this technology continues to evolve, its potential to transform industries and enhance human capabilities seems boundless.
Benefits of Digital Twins in Construction
Construction businesses are increasingly leveraging digital twins construction technology to enhance their workflows. Custom solution development allows for crafting specific types of digital twins tailored to meet the unique needs and requirements of each construction crew or project. This approach ensures that the technology provides maximum benefit and generates significant value for the business. Digital twins in construction offer a range of advantages crucial for the efficiency and success of construction projects.
Digital twin technology in construction enables precise modeling and simulation of construction projects. These digital twins serve as detailed, virtual representations of a project, allowing teams to visualize every aspect of a build, from initial design to final construction. This visualization aids in identifying potential design conflicts or construction issues early in the process, saving time and resources.
Moreover, digital twin building technology enhances project management and operational efficiency. By integrating real-time data from the construction site into the digital twin, project managers gain valuable insights into the project's progress. This integration allows for better resource allocation, scheduling, and risk management, leading to more efficient project execution.
Applying digital twin building technology in construction fosters improved collaboration and communication among project stakeholders. With a shared, accurate virtual project model, all parties — including architects, engineers, and contractors — can synchronize their efforts more effectively. This synergy helps reduce errors, ensuring all project components align with the planned design and specifications.
1. Enhanced Data Transparency and Availability
The construction industry, grappling with data access challenges, faces a complex scenario where essential data becomes fragmented across numerous stakeholders and software systems during the building process. This fragmentation hinders seamless access to crucial information.
In response to this challenge, the industry has increasingly adopted the Building Information Model (BIM) and digital twin technology. BIM is a unified source of truth that consolidates data and improves collaboration. The integration of digital twins in construction further enhances this framework.
Digital twins in construction provide a robust platform for real-time data aggregation in a single space. These digital twins automatically track actions and changes by leveraging smart sensors and IoT, significantly improving process transparency and data exchange among stakeholders. This technology revolutionizes the way data is managed, providing a dynamic, up-to-date model of the construction project.
The combination of BIM and digital twin construction technology in construction offers an innovative approach to tackling data accessibility issues. By ensuring that all relevant data is accessible within these integrated systems, the construction process becomes more efficient, transparent, and collaborative. This technological synergy is pivotal in transforming the construction industry's approach to data management and project execution.
2. Real-time Monitoring and Analysis
Implementing digital twin technology in the construction industry signifies a paradigm shift towards enhanced process efficiency. At the heart of this concept is the continual availability of real-time data, which presents many advantages in construction projects. These digital twins, powered by a combination of Internet of Things (IoT), Cyber-Physical Systems (CPS), and Artificial Intelligence (AI), offer invaluable real-time insights. Moreover, they establish a rapid closed-feedback loop that ensures comprehensive on-site activity capture, tracking, and analysis.
Digital twins in construction function as advanced tools for gathering and processing continuous data throughout the operational phases of a project. This capability is beneficial for immediate project needs and creates a rich database of information for future construction endeavors. One of the key benefits of digital twin technology in construction is its ability to monitor and control resource consumption, such as water and electricity, during both the building and accommodation stages. This function aids in optimizing resource utilization and reducing wastage, leading to more sustainable construction practices.
Additionally, digital twin building technology extends its utility to monitoring critical elements like generators, electrical distribution boards, and water levels in wells or pumps. This constant vigilance ensures that all systems function within their optimal parameters, preempting potential issues and facilitating timely interventions. Another significant application of digital twins in construction is the ongoing monitoring and control over project progress. This aspect is crucial for ensuring the construction adheres to contract documents and established norms, maintaining high quality and compliance standards.
In the long run, integrating digital twin technology into the construction process revolutionizes how projects are managed and executed. From creating a dynamic digital twins construction model that mirrors every aspect of the physical project to utilizing digital twin-building techniques for efficient resource management, the impact of digital twins is multifaceted. These digital replicas enhance operational efficiency and contribute to the sustainability and quality of construction projects.
3. Improved Collaboration
Efficient collaboration, communication, and cooperation form the backbone of successful construction projects. However, achieving these elements can be challenging, especially when multiple contractors and stakeholders are involved. Digital twin building technology offers a transformative solution to this challenge. It acts as a unifying platform, bridging the gap between various parties involved in a construction project.
Digital twin building technology creates a cohesive, accessible environment by perfectly synchronizing physical and virtual assets. This harmonized space is invaluable for owners, designers, contractors, and tradespeople, enabling them to collaborate effectively and maintain a unified understanding of the project's current status.
Integrating digital twins in construction revolutionizes how stakeholders interact with the project. It allows all critical specialists to quickly and accurately assess the project's situation. This immediate access to information is crucial, especially when addressing emergencies or resolving issues. With digital twin construction technology, the time-consuming data-gathering and analysis process is significantly reduced.
Furthermore, digital twin-construction models serve as a single source of truth. They offer a real-time, comprehensive view of the construction project, ensuring every stakeholder accesses the same information. This consistency is critical for maintaining project alignment and avoiding misunderstandings or errors arising from disparate data sources. Using digital twin-building techniques also enhances the ability to foresee potential problems and implement proactive measures, thereby minimizing delays and cost overruns.
4. Ability to Test What-If Scenarios
The advent of artificial intelligence has opened new avenues for testing various scenarios in numerous fields, including construction. However, the reliability of these predictions hinges on the accuracy and precision of the data used. In this context, digital twin building technology becomes an invaluable asset. Digital twins can provide precise and relevant information by continuously collecting real-time data. This capability is crucial for simulating potential outcomes and assessing risks accurately, which is essential in the dynamic environment of construction projects.
Digital twin technology offers enhanced prediction capabilities, fundamentally transforming how construction companies approach project planning and management. These companies can now design and construct new spaces more efficiently using data harvested from previous projects. Digital twins construction technology enables a more informed prediction of project progression, considering various factors that impact construction timelines and outcomes. This foresight is instrumental in optimizing resource allocation and scheduling, leading to more streamlined project execution.
Moreover, digital twin-construction models play a pivotal role in decision-making processes. Before implementing any changes or new strategies, specialists can use these models to visualize and analyze the potential outcomes. This data-driven approach, facilitated by digital twin-building methods, significantly departs from traditional reliance on intuition or assumptions. It allows for a more calculated and informed strategy, reducing the risk of costly errors and ensuring that solid, real-time data back every decision.
5. Enabled Preventive Measures
Implementing digital twin technology in construction significantly enhances a preventive approach to disasters or accidents, fundamentally altering how risks are managed on construction sites. With the capability to rigorously test different scenarios, digital twin building technology becomes instrumental in detecting anomalies or potential hazards. Upon identifying such risks, digital twins issue notifications, enabling timely interventions to prevent accidents. This advanced warning system allows construction specialists to maintain on-site safety, avoid errors in the as-built phase, and significantly reduce the need for subsequent rework.
Furthermore, the widespread availability of data through digital twins in construction encourages stakeholders to adopt a more proactive approach to their operations. This enhanced monitoring and data analysis allows for closer supervision of ongoing activities on the construction site. Stakeholders, equipped with real-time insights provided by digital twin construction technology, can intervene promptly to avert potential issues. This proactive stance marks a shift from reactive strategies that typically occur post-disaster to a more efficient and preventative operational model.
Integrating digital twin technology in construction projects offers a multi-faceted approach to project management. Not only does it contribute to the prevention of accidents and disasters through early detection and intervention, but it also facilitates a more comprehensive understanding of the construction process. By harnessing the power of digital twin technology, construction teams can ensure that projects are executed more safely, efficiently, and with a higher degree of accuracy. So, this technology's ability to simulate, monitor, and predict outcomes in construction projects represents a significant advancement.
6. Increased Accuracy
Harnessing digital twin technology in construction dramatically enhances operational accuracy, owing to its capability for real-time data flow and continuous updates. At the outset, this technology allows construction specialists to collect and analyze precise data from the site. This accurate data collection is fundamental for verifying the progress of construction projects, ensuring that every detail aligns with the initial plan.
Additionally, digital twins create a vital link between the tangible aspects of the construction site and their digital models. This connection is essential in eliminating discrepancies that occur between the actual construction elements and their digital representations. Without this synchronization, the risk of data inaccuracies could lead to significant project setbacks.
Implementing digital twins in construction also plays a pivotal role in developing robust databases. These databases are crucial for future project planning, enhancing decision-making processes, and guiding the adoption of more efficient, data-driven strategies. By relying on the comprehensive data provided by digital twins, construction professionals can approach project development with greater precision and foresight.
By providing real-time, accurate data and bridging the gap between physical construction and digital models, digital twins improve the accuracy of construction projects and pave the way for more sophisticated and effective project management strategies. As the construction industry continues to evolve, the influence of digital twin building technology is set to become increasingly significant, reshaping traditional construction methodologies.
Challenges and Limitations of a Digital Twin in the Construction Industry
Despite holding promise for the construction industry, digital twin implementation becomes a severe challenge for businesses that decide to develop and adopt the solution. For most firms, such a project might become the first initiative of enhanced digitalization, and the lack of relevant experience and expertise hinders the implementation success.
However, with the help and guidance of a reliable tech vendor, any construction firm can mitigate possible risks and resolve arising difficulties. Based on our experience, we gathered a list of the main challenges and limitations you should know about when considering cooperation with software development companies.
Data management
Data quality determines the outcomes of a venture such as digital twin implementation. Practitioners in the construction industry mention dozens of data-related aspects that appear to be a challenge during digital twin deployment, e.g., data analytics, data accessibility, data capturing, data ownership, data security, etc. Therefore, putting data in order and adequately organizing the data management process should be a preparation stage for the implementation of digital twin technology.
Cost uncertainties
A digital twin implementation is usually a long-term and complex project that demands significant resources to succeed. Without previous experience with digital transformation projects in the industry and relevant tech knowledge, executives might struggle to comprehend the full cost of the initiative and understand the value that a digital twin solution can bring to the company. These factors can generate numerous doubts and resistance to the implementation project.
Lack of standardization
Digital twin technology takes construction projects to a more advanced level of operations, so a development company should have a sufficient technical and operational basis to support that. Unfortunately, construction firms might struggle with process and data standardization, stakeholder training, infrastructure state, connectivity, and interoperability. Therefore, it is essential to approach the implementation strategically and transform the processes across the whole workflow.

How Does a Digital Twin Operate in the Construction Industry?
In construction, digital twins go hand in hand with BIM. The latest covers the creation of a 3D digital model that can be used to visualize future buildings or structures, simulate the building's behavior, predict quantity take-offs, detect clashes, etc. In turn, digital twin technology enhances BIM capabilities through real-time data gathered with the help of IoT devices and smart sensors.
Digital twin building technology synchronizes digital BIM models with physical buildings, creating an analytics edge. This powers up efficient data alignment that happens immediately, as specialists get a chance to constantly monitor construction progress and access decision-impacting insights on the go. Hence, instead of trying to fix mistakes after the fact, construction firms can detect and address them instantly.
How to Create a Digital Twin for Construction?
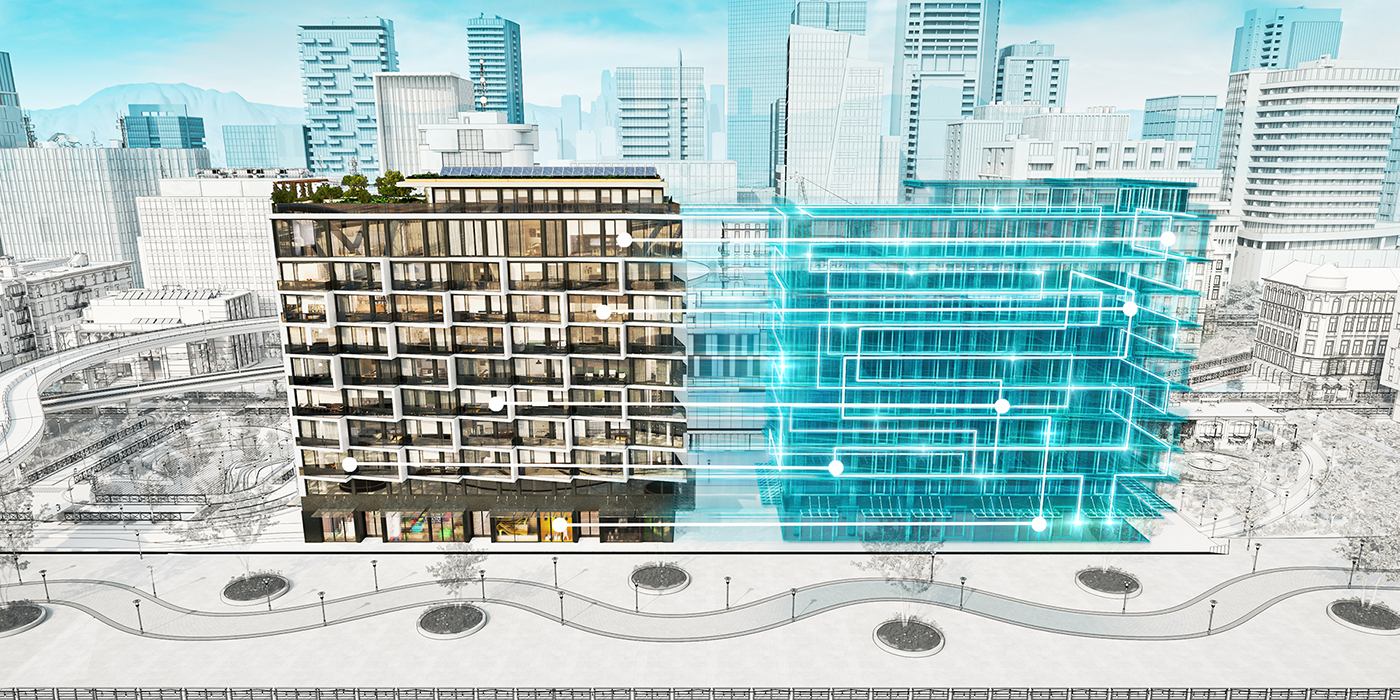
Creating digital twins for the construction industry demands collaborative efforts from all stakeholders involved in the building process. Owners, designers, architects, contractors, and trades should understand the technology's value and the changes it brings.
At the same time, software developers account for the main scope of work in digital twin development. Their experience and domain expertise are key to successful deployment and implementation. So, when considering developing a digital twin for your construction firm, you should start by partnering with a reliable vendor. Then, they will guide you through the development stages, which will likely look like this.
Objective definition: understanding the purpose of your digital twin initiative and determining what aspects of the construction you will track through the technology.
Data requirements establishing: determining what data you need to build a digital twin, e.g., BIM models, design drawings, data from IoT devices and sensors, etc.
BIM model creation: designing a 3D digital model of the desired building.
Real-time data incorporation: installing IoT devices and smart sensors at various locations to ensure real-time data flow regarding construction progress and building state.
Data integration and visualization: connecting the prepared BIM model with the real-time data within one platform and visualizing the physical asset in a digital environment.
Validation: calibrating digital twins construction after its launch to guarantee accuracy by comparing the insights it provides with the physical asset.
Continuous monitoring and analysis: leveraging the real-time data to run analysis and make data-driven decisions.
Maintenance and updates: feed relevant and up-to-date data to ensure the digital twin's correct work and accurate insights.
How to Use Digital Twins in the Construction Industry?
A construction digital twin building technology is a versatile tool you can tailor to keep track of every event within your construction site. However, our practical knowledge shows that applying the solution and generating real value might be hard when you have so many options. Hence, we gathered some interesting use cases you can try for your business.
- design visualization;
- clash detection;
- construction planning and sequencing;
- safety planning and training;
- progress monitoring and reporting;
- predictive maintenance;
- energy efficiency analysis;
- facility management;
- retrofitting and renovation;
- lifecycle performance analysis.
Digital Twin Examples in Construction
Despite the challenges we have mentioned in the article, dozens of firms and institutions have already been leveraging digital twins to enhance their performance and improve the outcomes of their work. Here are some of the most vivid examples.
Morandi Bridge in Italian Genoa
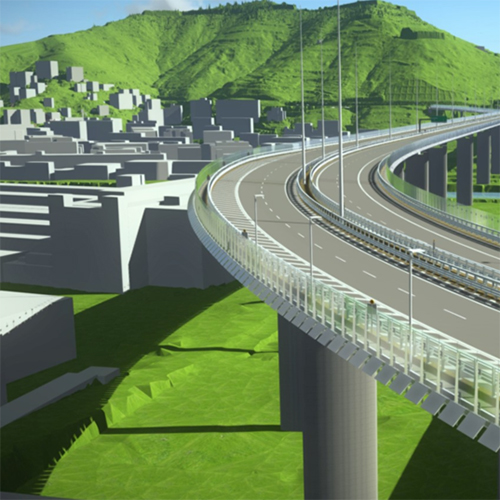
Italferr S.p.A, part of the Italian State Railways Group, used BIM models and created a digital twin workflow to streamline the rebuilding of Morandi Bridge, a crucial link between Italy and France's road systems. Implementing the technology allowed the company to ensure accurate design, promote efficient collaboration between a multidisciplinary project team, and ensure a single source of truth.
LAX
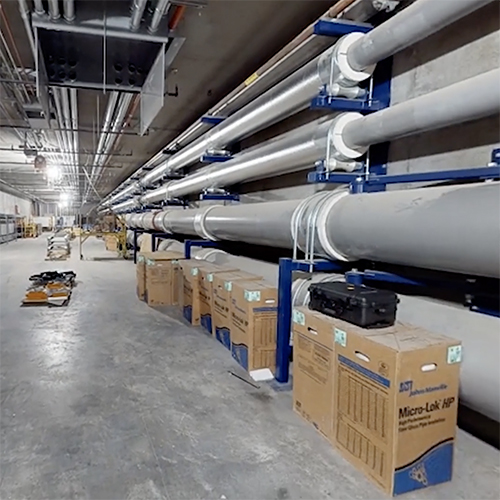
An architecture and design firm Corgan used a digital twin technology while reconstructing Los Angeles International Airport (LAX) to optimize performance. With the help of technology, the company managed to capture the existing conditions of the building, which helped them to collaborate efficiently through the reconstruction process. Corgan also shared the 3D digital twin with facility owners, powering advanced facility management.
Smart Cities
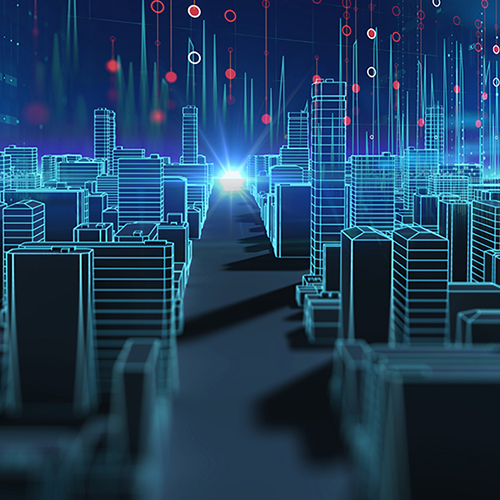
The popularity of digital twinning for whole cities is growing, and more and more metropolitan areas or even small towns get virtual replicas. The value of such digital twins is enormous, as they allow for the planning of more sustainable and eco-friendly construction, reducing carbon emissions, organizing traffic, etc. Overall, a full-scale city digital twin has the potential to improve its dwellers’ lives and create more environment–friendly spaces.
Build Your Digital Twin with Program-Ace
The digital twin technology in construction is a game-changer that brings a new era of operations and approaches. So, to get ahead of the competition and secure your place as a leader in the industry, consider implementing a digital twin construction into your workflow for better performance, collaboration, and prediction.
Program-Ace, an experienced software development service provider, is ready to guide your construction business's digital transformation. Feel free to contact us and figure out your plan for harnessing the digital twin value.