Leading factories around the globe have seamlessly integrated cutting-edge technologies into their daily operations, underlining the manufacturing sector's commitment to achieving a higher level of automation and digitalization. These advancements are pivotal in enhancing product design and production workflows, accelerating the journey from concept to market, and significantly lowering operational costs. Adopting sophisticated solutions, including artificial intelligence, robotics, the Internet of Things (IoT), and advanced data analytics, is crucial in attaining these objectives.
Among these technologies, digital twins stand out as a foundational element of intelligent manufacturing, offering substantial benefits to businesses within the sector. A digital twin in manufacturing refers to a virtual model that mirrors a physical object or process. This technology simulates, analyzes, and optimizes manufacturing systems and processes. By understanding what a digital twin in manufacturing entails, companies can leverage this technology to anticipate issues, test scenarios, and improve overall efficiency without interrupting actual production.
A digital twin development company specializes in creating these sophisticated virtual models, which are becoming increasingly crucial in the manufacturing industry. The role of a digital twin in manufacturing extends beyond mere replication; it encompasses real-time monitoring, predictive maintenance, and operational optimization. By employing a manufacturing digital twin, businesses can better understand their operations, leading to more informed decision-making and enhanced product quality.
The significance of digital twins in the manufacturing sector cannot be overstated. As companies strive to maintain competitiveness, the adoption of a manufacturing digital twin becomes a strategic necessity. These virtual replicas enable manufacturers to bridge the gap between the physical and digital worlds, facilitating a seamless flow of information and a more agile response to market demands.
What Is a Digital Twin in Manufacturing?
Incorporating digital twin technology into production ushers a new age of efficiency and creativity. By establishing virtual equivalents to actual systems, manufacturers gain unprecedented insights and control over their operations.
Definition. A digital twin in manufacturing refers to a virtual replica of a physical manufacturing process, product, or system. This technology enables the simulation, analysis, and optimization of manufacturing operations in a digital environment, facilitating real-time monitoring and predictive maintenance without disrupting production.
Components. The structure of a digital twin encompasses real-time data collection, advanced analytics, and machine learning algorithms to accurately mirror the physical state of manufacturing assets. It integrates seamlessly with IoT devices and sensors embedded in manufacturing equipment, ensuring the digital twin receives up-to-date information from its physical counterpart.
Functionality. A digital twin's primary function in manufacturing is to improve operational efficiency and product quality. It achieves this by enabling manufacturers to run simulations, predict potential failures, and test changes in a risk-free virtual setting, thereby reducing downtime and optimizing production processes.
Benefits. Implementing a manufacturing digital twin offers numerous advantages, including enhanced decision-making through data-driven insights, increased production efficiency, and reduced costs associated with unscheduled maintenance and machine downtimes. Moreover, it supports the development of more sustainable manufacturing practices by identifying areas where resources can be used more efficiently.
Implementation. Deploying a digital twin in manufacturing settings requires a collaborative effort between IT specialists, data scientists, and manufacturing engineers. The process involves mapping the physical manufacturing system, selecting appropriate sensors and IoT devices for data collection, and developing a digital twin model that accurately reflects the physical world.
Future prospects. As digital twin technology continues to evolve, its application in manufacturing is expected to become more widespread, driving further innovation and efficiency. The ongoing integration of digital twins with other technologies, such as AI and augmented reality, is set to enhance their capabilities, making them an indispensable tool in the future of manufacturing.
Thus, the implementation of digital twin technology marks a transformative step for the manufacturing sector, offering a dynamic tool for optimizing production and driving forward technological advancement. As manufacturers continue to harness the power of digital twins, the boundaries of what is possible in manufacturing will undoubtedly expand, ushering in a future where digital and physical realms converge seamlessly for unparalleled operational excellence.
The Concept of Digital Twins in Manufacturing Explained
The emergence of digital twins traces back to the early 1990s, with their public debut occurring in the 2000s and a significant rise in popularity over the last decade. Advances in technology have played a crucial role in this surge, making high-speed internet, interconnected systems, and artificial intelligence more accessible and affordable for a wide range of companies.
A digital twin in manufacturing is a detailed virtual model of a physical asset, such as a product, equipment piece, or an entire production system. The defining characteristic that sets a digital twin apart from a simple digital replica is its capability to update in real time. It maintains a continuous data flow from its physical counterpart, adapting to changes in real-world conditions and thereby existing at the intersection of physical reality, its digital representation, and the data link that connects them.
Technological foundations of any digital twin include 3D modeling and VR/AR for precise virtual visualization, IoT sensors for gathering real-time data from the physical world, and artificial intelligence to analyze the vast amounts of data generated during the operation of a digital twin.
In manufacturing, digital twins serve as invaluable assets for enhancing decision-making processes, boosting operational efficiency, and minimizing errors. They enable manufacturers to perform virtual testing, anticipate potential failures, and refine production processes, thus ensuring that manufacturing operations are robust and flexible.
Embracing digital twin technology marks a significant evolution in manufacturing, moving toward more intelligent, data-informed production ecosystems. By integrating digital twins, manufacturers are able to merge physical and digital processes seamlessly, ushering in a new era of precision, productivity, and innovation in manufacturing practices.
Digital Twins As One of the Pillars of Smart Manufacturing
Smart manufacturing redefines production workflows by introducing solutions that overcome the rigidity of traditional methods, focusing on enhanced adaptability and flexibility. The shift towards smart manufacturing is driven by the adoption of advanced automation technologies and data analytics, aiming to optimize manufacturing outcomes.
The discussion around digital twin technology in manufacturing aligns closely with the objectives of smart manufacturing. The digital twin in manufacturing has become a key topic of interest due to its potential to transform conventional manufacturing processes. A smart manufacturing digital twin offers a detailed virtual representation of a physical manufacturing process or system, enabling real-time monitoring and predictive analysis.
With smart manufacturing, detailed oversight of the production process is now possible at every stage, from raw material to finished product. This level of monitoring marks a significant departure from traditional methods, where defects might only be identified after production completion. The use of a manufacturing digital twin enhances process management by improving real-time visibility and adding predictive capabilities to the manufacturing workflow.
Digital twins in manufacturing serve as advanced simulation tools, allowing companies to identify potential issues and explore various operational hypotheses. This simulation capability is critical for identifying optimization opportunities and implementing efficiency-enhancing strategies. Through the strategic application of a digital twin, manufacturing operations can simulate different production conditions, evaluate the potential impacts of changes, and adopt improvements that enhance both product quality and process efficiency.
The adoption of digital twin technology in smart manufacturing represents a significant advancement in the way production processes are managed and optimized. By integrating digital twin technology, manufacturers can achieve a higher level of precision and efficiency in their operations, leading to improved adaptability and performance in the manufacturing sector. As the industry evolves, the function of digital twins in improving production processes becomes more important, emphasizing their significance in the continuous digital transformation of manufacturing.

Benefits of Digital Twin in Manufacturing
The value of digital twin technology in the manufacturing sector is significant, unlocking numerous opportunities for businesses to explore. This technology enables manufacturers to observe and manage their operations at different stages and from multiple perspectives, paving the way for substantial improvement. Here are the key benefits that digital twins offer:
Real-time insights. Digital twins in manufacturing provide a live view of the production process, enabling immediate adjustments and enhancements.
Predictive analysis. A manufacturing digital twin aids in foreseeing potential issues and minimizing downtime and maintenance efforts.
Process efficiency. Companies can test and refine operations by employing a digital twin in manufacturing, boosting productivity and reducing waste.
Using digital twin technology represents a strategic move for manufacturers seeking to innovate and optimize their production landscapes.
1. Enhanced Production Performance
At the heart of digital twin technology, mainly when applied in manufacturing, lies the objective of enhancing optimization and driving improvements. A digital twin in manufacturing acts as an exact virtual mirror of an asset or process, enabling the identification and illustration of inefficiencies in process design, material utilization, energy consumption, and more, all without interrupting actual production activities. Consequently, this eliminates bottlenecks that may have previously gone unnoticed or unaddressed, significantly boosting factory efficiency.
Employing a digital twin in manufacturing settings not only spotlights areas for enhancement but also facilitates a proactive approach to maintaining operational excellence. By leveraging a manufacturing digital twin, businesses can anticipate challenges before they impact the production line, ensuring continuous improvement and innovation.
Moreover, integrating a digital twin into the manufacturing process embodies a strategic tool for refining production workflows. It offers a dynamic platform for simulating various scenarios, testing hypotheses, and implementing solutions that lead to substantial operational advancements.
All in all, a manufacturing digital twin transforms traditional manufacturing practices. It provides a comprehensive and accurate representation of manufacturing processes, empowering companies to achieve higher productivity and operational efficiency. Through the strategic application of digital twin technology, manufacturers unlock the potential to revolutionize their production systems, setting new standards for excellence in the manufacturing industry.
2. Improved Product Quality
In the manufacturing sector, digital twin technology revolutionizes product development by eliminating the need for traditional prototyping stages. Rather than allocating resources to construct physical models, manufacturers increasingly adopt digital twins, which offer a more flexible and manageable approach. This shift allows product design, testing, and quality assurance processes to consume fewer resources while ensuring greater adaptability, efficiency, and accuracy, culminating in enhanced product quality.
With the implementation of a digital twin in manufacturing, the entire product lifecycle, from conception to production, becomes more streamlined and cost-effective. A twin in manufacturing provides a detailed virtual representation that can be easily adjusted and tested in various scenarios, significantly reducing the time and expense associated with physical prototyping.
Additionally, a manufacturing digital twin facilitates a deeper analysis and understanding of product performance under diverse conditions. This capability accelerates the innovation cycle and improves the final products' reliability and durability.
The strategic application of digital twin technology in the manufacturing digital landscape transforms how products are conceived, designed, and brought to market. By leveraging digital twins, manufacturers can achieve higher precision and quality in their products, setting new standards for excellence in the manufacturing industry.
Overall, integrating digital twin technology into manufacturing processes represents a significant leap forward, enabling businesses to optimize their operations and deliver superior products with greater efficiency and reduced costs.
3. Decreased Product Time-to-Market
Embracing digital twin technology in the manufacturing sector marks a significant departure from the reliance on physical prototypes, drastically cutting down the timeline from initial design to final product realization. Manufacturers can expediently evaluate their product designs through direct access to insights and predictive analyses that digital twins provide. Such immediate feedback enables quick adjustments at the conceptual phase, sidestepping traditional delays.
Digital twins in manufacturing are virtual counterparts of physical products, allowing for comprehensive scenario simulations and performance assessments without physical prototypes. The capacity to conduct these virtual tests and analyses significantly enhances design accuracy and product reliability, minimizing the risk of expensive post-production modifications.
Applying a digital twin in the manufacturing process injects unparalleled flexibility and efficiency into product development. Real-time design modifications, informed by the digital twin's feedback, negate the slowdowns associated with physical prototyping. This responsiveness is crucial in meeting the rapid pace of market demands and maintaining a competitive edge through continuous innovation.
4. Prolonged Equipment Longevity
Equipment wear and unexpected breakdowns significantly disrupt manufacturing operations. Digital twins offer manufacturers advanced capabilities to maintain their machinery optimally by enabling continuous monitoring and predictive maintenance scheduling. Utilizing digital twin technology in manufacturing settings protects assets and tools from avoidable damage, ensuring equipment delivers its total designed value.
Digital twins in manufacturing provide a detailed overview of equipment health, allowing for the early detection of signs of wear or potential failures. This foresight enables timely interventions, preventing costly downtime and extending equipment life. By adopting a digital twin, manufacturing operations gain the advantage of enhanced reliability and efficiency in their machinery management practices.
Furthermore, applying a manufacturing digital twin contributes to more thoughtful, data-driven decision-making regarding maintenance. Predictive analytics derived from digital twins allow maintenance to be conducted just in time, avoiding unnecessary preemptive maintenance and unexpected equipment failures. This strategic approach ensures manufacturing processes remain uninterrupted, maximizing productivity and asset utilization.
5. Improved Business Profitability
Merging the comprehensive advantages of digital twin technology in manufacturing yields a multifaceted outcome — enhanced business profitability. The diligent application of constant monitoring and optimization strategies, alongside meticulous equipment maintenance facilitated by digital twins, plays a pivotal role in elevating product quality and diminishing the prevalence of defective items. These improvements lead to a notable reduction in operational costs, particularly when viewed through a long-term lens.
Deploying a digital twin in manufacturing settings ushers in a new era of precision and efficiency. By taking advantage of the power of digital twins, manufacturers can ensure their machinery operates at peak performance, thereby preventing unnecessary downtimes and extending the lifespan of their assets. This proactive approach to maintenance, underpinned by the insights gleaned from a digital twin, contributes significantly to cost savings and operational sustainability.
Furthermore, the ripple effects of integrating a manufacturing digital twin extend beyond mere cost reduction. Enhanced process control and quality assurance measures, made possible by the detailed analytics provided by digital twins, bolster your brand's reputation. This elevation in quality and reliability fosters more substantial relationships with clients, laying the groundwork for increased customer loyalty and the potential for expanded business opportunities.
6. Innovation Encouragement
Incorporating a digital twin into your manufacturing operations serves as the gateway to the dynamic world of smart manufacturing, offering an array of unparalleled advantages and opportunities for your business. The strategic utilization of this cutting-edge technology can pave the way for a remarkable success narrative, positioning your company at the forefront of innovation. Such an achievement becomes particularly valuable when presenting a compelling case to garner support from upper management or investors for your innovation initiatives.
A digital twin in manufacturing is not merely a tool but a transformative force that redefines conventional practices. Creating a virtual counterpart of your physical assets and processes unlocks the potential for data-driven decision-making and optimization. Integrating a manufacturing digital twin into your operations empowers you with real-time insights, predictive analytics, and the ability to simulate various scenarios, resulting in more agile and efficient processes.
Furthermore, applying a digital twin extends beyond operational improvements; it can potentially revolutionize your business ecosystem. From enhancing product development cycles to streamlining supply chain management, digital twins impact multiple facets of your organization. This holistic approach to digitalization fosters resilience and adaptability, enabling your company to thrive in today's rapidly evolving business.
Cooperate with us to successfully implement digital twins solutions for your business.
Digital Twin Use Cases in Manufacturing
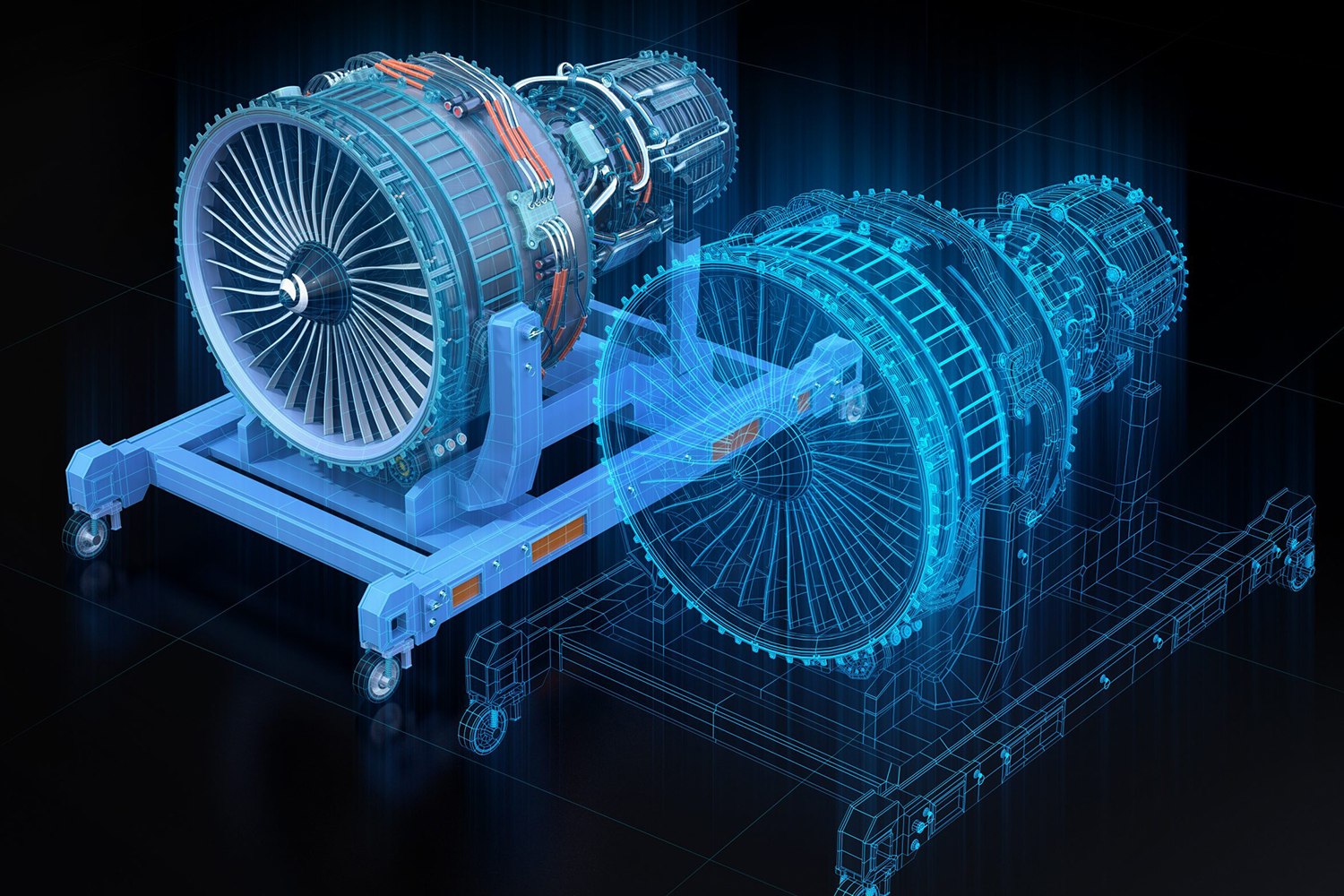
Examples of digital twins in manufacturing are numerous and applicable to the building of different products, e.g., automotive, aerospace and aviation, pharmaceutical, consumer goods, medical devices, etc. Here are the most common ideas of how you can leverage a digital twin in smart manufacturing.
Predictive Maintenance
Predictive maintenance is an extremely powerful tool for manufacturers to switch to early detection of any faults, precise diagnosis, and preventing equipment downtown before it happens. The use of a digital twin for predictive maintenance in manufacturing gives a previously unapproachable level of visibility and transparency to equipment monitoring.
So how does this technology work? It all starts with IoT sensors being connected to every component of an equipment piece or system. The aforementioned sensors track each aspect of operation and record and log an incident if any of the components fail. In the course of time, the logs show a certain pattern that is later going to be used to predict future breakages and arrange maintenance accordingly.
Product Quality Monitoring & Testing
Digital twins change product quality assurance, reducing the financial risks of spending extra on testing. By transferring this process into the simulation, manufacturers can orchestrate different scenarios and implement changes in a reactive environment, where they are not constrained by physical limitations and aren’t dependent on physical labor or a limited budget for testing.
Some businesses evolve even further as they start to converge digital twins and metaverse and leverage their custom-built industrial virtual world to test their products more quickly and cost-efficiently. For industries like automotive, this crucially changes product testing approaches. Manufacturers don’t need to spend time and money to build physical prototypes of new vehicle models, and test drivers no longer experience any risk to their life and health.
Production System Design Optimization
A digital twin example in manufacturing can go beyond a point solution solely engaging a product or a separate equipment piece. Manufacturers can simulate a whole production system, namely a production line, to assess and test a certain layout for its efficiency. This way, you can detect bottlenecks and risks before actually setting up new lines and redesign them accordingly, ensuring that the most efficient option will be implemented.
At the same time, you can use the same approach to optimizing systems and processes on-site (warehouse design) and outside the factory (supply and delivery chains). Digital twins allow manufacturers to simulate any process they want to inspect, significantly increasing the amount of available data applicable for optimization.
Asset Lifecycle Management
A digital twin created for a certain asset stays relevant for its entire lifecycle, from initial production to final release to the world. Moreover, some manufacturers, namely developers of vehicles and heavy machinery, don’t stop there and keep tracking the product even after it is sold to the end-point user to provide adequate maintenance and support.
There is another significant, but not as obvious, advantage. As you can see, digital twins and data access are inextricably linked. For manufacturers that are constantly fighting with data loss, digital twins become a guarantee of asset data being preserved, organized, and available at any point in time.
Safety Enhancing
One of the underused implementation cases is leveraging digital twins to improve safety on-site. The never-stopping equipment and environment monitoring, when used right, can reduce the chance of accidents happening and protect workers from getting injuries.
Such a result is possible due to several outcomes generated by digital twins' implementation. First, enhanced tracking and visualization of assets allow for detecting issues remotely, decreasing the interactions between workers and faulty equipment. Second, predictive maintenance reduces breakages and increases equipment efficiency, which also minimizes crew exposure to hazardous conditions.
How Top Manufacturers Leverage Digital Twins in Their Practice
Nowadays, digital twins are no more just a promising but unrealistic concept but a real-life solution a lot of companies have already implemented in their work. Here are some most interesting cases of how top manufacturers apply the technology.
Tesla
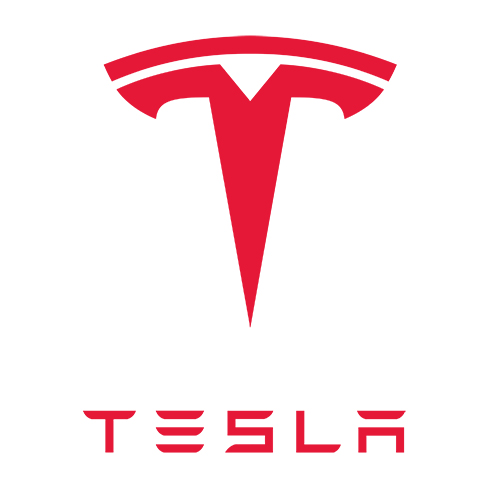
It is no wonder that Tesla, one of the most innovative automotive manufacturers, has been using digital twins for quite some time. It is reported that every Tesla vehicle has its own digital twin powered by IoT sensors. They constantly gather data on the vehicle’s state to predict when a breakage can happen. This way, the company manages to decrease expenses on serving cars on warranty and provide a better customer experience to Tesla’s owners.
Unilever
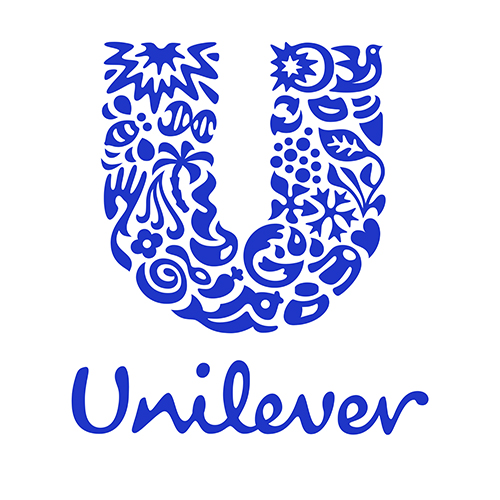
This world leader in consumer goods production leverages digital twins to create virtual copies of their factories and gain better visibility and control over the processes, equipment, and products. The mass implementation of the digital twins allowed the enterprise to access a lot of game-changing advantages, for example, optimization of time required for batch production, automation of repetitive manual tasks, improvement of products’ quality etc.
Boeing
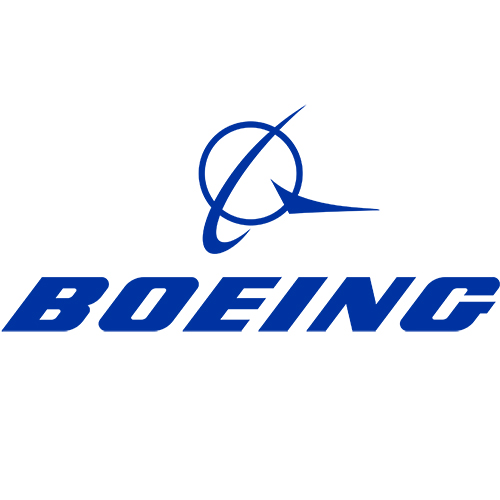
The Boeing team uses digital twins for aircraft designing, as they power up the simulation with the data related to the performance of various plane parts over their lifecycle. This allows engineers to predict when components may fail and make necessary improvements to increase the quality. At the same time, the company also applies digital twins to determine a perfect cargo load balance and understand the true capacities of a certain aircraft.
Kaeser
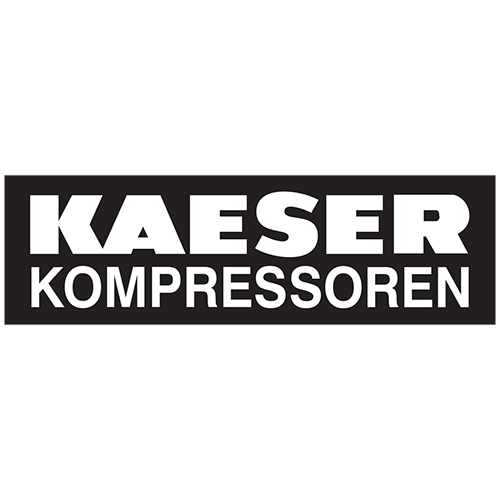
Kaeser, a German manufacturer of compressed air products, leveraged digital twins to adopt an as-a-service business model instead of simply selling their products to users. Digital twins allow the company to get data on air consumption rates and charge users accordingly, simultaneously tracking the state of the equipment and implementing predictive maintenance measures to prevent failures.
Build Your Digital Twin for Manufacturing with Program-Ace
The variety of digital twin manufacturing examples proves the versatility and practicability of the technology. In a world where the competition is constantly growing and more businesses are choosing to utilize advanced technologies, digital twins can give a boost to your manufacturing business and offer solutions to the issues that prevent your scaling.
However, digital twin implementation can only make a difference when done right. Program-Ace, a leading software development service provider, knows how to apply digital twin technology and extract maximum value from it for manufacturing businesses. Feel free to contact us for details and discuss what opportunities our cooperation can bring to your company.